Основы плазменной резки. Что такое плазменная резка
Основы плазменной резки
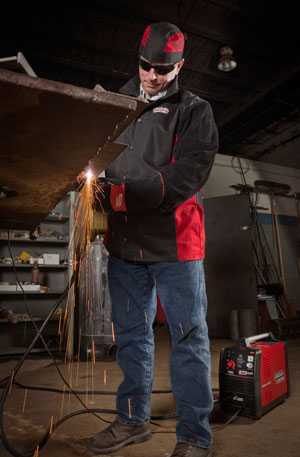
Что такое плазменная резка?
Процесс плазменной резки основан на использовании высокоскоростного потока ионизированного газа, поступающего из сужающегося отверстия. Этот ионизированный газ, т. е. плазма, служит проводником электричества от плазменной горелки к рабочему изделию. Плазма нагревает рабочее изделие и плавит материал. Кроме этого высокоскоростной поток ионизированного газа механически сдувает расплавленный металл и тем самым разделяет материал.
Каковы преимущества плазменной резки перед кислородно-газовой?
Плазменная резка подходит для любых токопроводящих металлов – например, углеродистой стали, алюминия и нержавеющей стали. В случае углеродистой стали резка отличается большей скоростью и шириной отверстий по сравнению с легированной.
Кислородно-газовая резка основана на сгорании, или окислении, металла. Следовательно, она применима только к стали и другим черным металлам, которые вступают в реакции окисления. Такие металлы, как алюминий и нержавеющая сталь, при этом образуют оксид, который замедляет и останавливает дальнейшее окисление, что делает традиционную кислородно-газовую резку невозможной. Плазменная резка не зависит от процесса окисления и поэтому также подходит для алюминия, нержавющей стали и любых других токопроводящих материалов.
Хотя для плазменной резки пригодны различные газы, сегодня для этого чаще всего используется сжатый воздух. Сжатый воздух легкодоступен и поэтому плазма не требует использования горючего газа и сжатого кислорода.
Для новичков плазменная резка обычно проще в освоении, а в случае тонкопрофильных материалов плазменная резка значительно быстрее кислородно-газовой резки. Однако для плазменной резки стали большого сечения (2,5 см и больше) требуются источники питания очень высокой мощности. Поэтому для таких случаев больше подходит традиционная кислородно-газовая резка, которая вдобавок в таких условиях обеспечивает большую скорость резки.
Для чего можно использовать плазменную резку?
Плазменная резка идеально подходит для резки стали и цветных металлов толщиной менее 2,5 см. Кислородно-газовая резка требует, чтобы для поддержания процесса окисления оператор тщательно контролировал скорость резки. Плазма в этом отношении более неприхотлива. Плазменная резка особенно хорошо подходит для некоторых узкоспециализированных задач, например, резки растянутых металлических пластин, что почти невозможно в случае кислородно-газовой резки. Если сравнивать с механической резкой, плазменная резка отличается значительно большей скоростью и пригодностью для нелинейной резки.
Какие ограничения имеет плазменная резка? В каких случаях предпочтительна кислородно-газовая резка?
Системы плазменной резки обычно имеют большую стоимость. Кислородно-газовые устройства не требуют доступа к сети питания и баллонам сжатого воздуха, что оказывается более удобно для некоторых пользователей. Кислородно-газовая резка больше подходит для резки изделий большого сечения (>2,5 см), так как в таких условиях она имеет большую скорость по сравнению с плазменными системами.
На что обратить внимание при покупке системы плазменной резки?Если Вы приняли решение о покупке системы плазменной резки, помните о следующем:
1. Определите, металл какой толщины Вам нужно будет разрезатьОдин из самых важных факторов, который Вам нужно определить – это толщина металла. Мощность большинства систем плазменной резки рассчитывается на основе производительности резки и силы тока. Следовательно, если чаще всего Вам приходится разрезать материал толщиной 6 мм, Вам подойдет устройство низкой мощности. Для резки металлов толщиной более 1,2 см нужен аппарат большей мощности. Даже если для этого подойдет менее мощная система, она не сможет обеспечить достаточное качество резки. Вместо этого разрез будет едва достигать другой стороны пластины и оставлять окалину и шлак. Для каждой системы существует оптимальный диапазон толщины материала – убедитесь, что он будет соответствовать Вашим задачам. Как правило, системы для резки по толщинам около 6 мм имеют мощность около 25А, 12 мм – 50-60А, 19-25 мм – 80А.
2. Выберите оптимальную скорость резкиКак будет проходить резка – в условиях производства или более свободной обстановке, где не так важна скорость? При покупке системы плазменной резки производитель должен предоставить информацию о скорости резки по различным толщинам, которая обычно указывается в сантиметрах в секунду. Даже если чаще всего Вам приходится заниматься резкой по небольшим толщинам (около 6 мм), более мощное устройство позволит провести резку быстрее. Опыт показывает, что для резки на производстве лучше всего выбирать устройства, которые позволяют вести резку по толщинам примерно в два раза больше обычной. Например, для того, чтобы быстро и качественно выполнять продолжительную резку стали толщиной 6 мм, рекомендуется использовать систему с максимальной глубиной резки 1,2 см (мощностью 60А).
Если Вы планируете продолжительную автоматическую резку, обязательно узнайте о рабочем цикле аппарата. Рабочий цикл обозначает, как долго можно вести непрерывную резку до перегрева аппарата или горелки. Рабочий цикл обозначают в виде доли 10-минутного периода. Например, рабочий цикл 60% при 50А означает, что вы можете вести непрерывную резку с мощностью 50А на протяжении 6 минут каждые 10 минут. Чем больше рабочий цикл, тем меньше время простоя.
3. Поддерживает ли устройство альтернативные методы зажигания дуги, помимо высокочастотного?В большинстве систем плазменной резки используется высокочастотная вспомогательная дуга, которая служит для образования электрического контура в воздухе. Тем не менее, высокочастотный ток может вызывать помехи в работе компьютеров и другого офисного оборудования. Поэтому альтернативные методы зажигания, которые позволяют избавиться от потенциальных проблем из-за высокогочастотного тока, могут оказаться более предпочтительными.
Например, метод зажигания точечным касанием электрода предполагает использование форсунки с постоянным током обратной полярности, внутри которой расположен электрод с током прямой полярности. Сначала форсунка и электрод соприкасаются. При нажатии триггера горелки между электродом и форсункой возникает электрический ток. После этого электрод отводят от форсунки, из-за чего образуется вспомогательная дуга. Когда вспомогательная дуга приближается к рабочему изделию, она преобразуется в режущую. Это преобразование вызывается разностью потенциалов форсунки и рабочего изделия.
4. Сравните стоимость и срок службы изнашивающихся деталейГорелки плазменной резки имеют множество изнашивающихся деталей, которые требуют регулярной замены. Поэтому постарайтесь найти производителя, который предлагает устройства с минимальным числом изнашивающихся деталей. Чем их меньше, тем меньше придется тратить на их замену.
Срок службы деталей должен быть указан в спецификациях от производителя. При этом учтите, что некоторые производители указывают эти данные в виде числа разрезов, а другие – числа зажиганий дуги.
5. Проведите испытания и оцените качество резкиПроведите пробные испытания нескольких устройств с одной и той же скоростью сварки и одинаковой толщиной материала, чтобы сравнить качество резки. При этом не забудьте убедиться в отсутствии окалины с нижней стороны пластины и том, что линия разреза расположена под заданным углом.
Горелка должна образовывать сфокусированную, жесткую дугу. Изнашивающиеся детали от Lincoln Electric специально разработаны так, чтобы сконцентрировать поток плазмы и собрать энергию в одной точке.
Также в качестве теста во время резки можно приподнять горелку над пластиной. Проверьте, насколько высоко Вы сможете поднять горелку до того, как разомкнется дуга. Длинная дуга означает большее напряжение и возможность резки по пластинам большой толщины.
6. Преобразование от вспомогательной к режущей и от режущей к вспомогательной дуге Преобразование от вспомогательной к режущей дуге происходит в тот момент, когда она приближается к рабочему изделию. Это зависит от разницы потенциалов форсунки и рабочего изделия. Обычно для создания этой разницы в используется большой резистор в контуре вспомогательной дуги. Она непосредственно влияет на максимальное расстояние, на которое может распространяться дуга. После того, как вспомогательная дуга переместится на рабочее изделие, с помощью переключателя (реле или транзистора) включается токовая цепь.
Поэтому Вам нужно устройство, которое обеспечит быстрый переход от вспомогательной к режущей дуге на большом расстоянии от рабочего изделия. Такие модели «прощают» ошибки оператора и лучше подходят для строжки. Хороший способ проверить характеристики трансфера – провести резку растянутого металла или просечно-вытяжной стали. В таких случаях дуга должна очень быстро преобразовываться из вспомогательной в режущую и обратно. При этом часто рекомендуют использовать только силу тока вспомогательной дуги.
7. Проверьте поле обзораВо время работы оператор должен хорошо видеть зону работ. Особенно это касается фигурной резки. Поле обзора зависит от геометрии горелки – маленькие, компактные горелки и удлиненные форсунки упрощают наблюдение за ходом резки.
8. ПортативностьМногие клиенты используют свои системы плазменной резки для нескольких задач, из-за чего им часто приходится перемещать аппарат по территории предприятия или даже перевозить его на другие заводы. Легкое, портативное устройство и средство транспортировки – например, тележка или наплечный ремень – могут это значительно упростить. Кроме того, в случае ограниченного пространства полезно иметь компактную модель.
Также удобно, когда устройство имеет место для хранения кабелей, горелок и изнашиваюихся деталей. Это значительно упрощает перевозку аппарата, потому что в противном случае такие аксессуары часто волокутся по земле и теряются.
9. НадежностьДля работы в тяжелых промышленных условиях нужны надежные устройства с защитой элементов управления. Например, защищенные соединения и разъемы горелок меньше изнашиваются. Некоторые модели также включают защитную решетку вокруг воздушного фильтра и других внутренних узлов. Эти фильтры имеют большое значение, так как они удаляют из сжатого воздуха масло и влагу, которые могут приводить к возниканию дуговых разрядов. Соответственно, эти фильтры важно защищать от повреждений.
10. Выясните, насколько легко и комфортно пользоваться аппаратомВыбирайте системы с большой удобочитаемой панелью управления. Такая панель позволяет пользоваться аппаратом даже тем, кто никогда не занимался плазменной резкой. Кроме того, работу с аппаратом значительно упрощают нанесенные инструкции на корпусе.
Удобно ли Вам держать в руке горелку? Она должна быть удобной и эргономичной.
11. Функции безопасностиПо возможности выбирайте модели с предохранительным датчиком наличия форсунки. Оно не позволит устройству работать без установленной форсунки. Некоторые системы безопасности можно обмануть и заставить «думать», что форсунка на месте, хотя это не так. Если при этом включить питание, оператор подвергнется риску поражения током напряжением 300В. Это невозможно при наличии датчика Lincoln.
Некоторые модели также имеют функцию предупреждения о включении горелки до зажигания дуги. Например, устройство может подать звуковой сигнал за три секунды до включения горелки, чтобы оператор успел убрать от нее все части тела.
Как пользоваться системой плазменной резки максимально эффективно?После того, как Вы выбрали подходящую систему плазменной резки, Вы можете повысить качество резки с помощью следующих подсказок:
1. Процедура настройкиПеред началом работы убедитесь в выполнении следующих условий:
Подача чистого сжатого воздуха без частиц влаги и масла. Быстроизнашивающиеся детали и черные отметины на пластине могут указывать на загрязненный воздухПравильное давление воздуха – оно показано на индикаторах устройстваПравильная установка форсунки и электродаРабочий зажим надежно зафиксирован на чистой строне рабочего изделия
2. Техника безопасностиВо время работы необходимо соблюдать технику безопасности. Прочтите руководство по эксплуатации. Вы должны хорошо понимать, как работает аппарат. Во время резки рекомендуется носить длинные рукава и перчатки, так как при этом образуются брызги расплавленного металла. Для защиты глаз необходимо пользоваться затемненными очками или сварочным щитком. Обычно при этом используются степени затемнения от 7 до 9. Также соблюдайте все приведенные в инструкции советы и рекомендации по технике безопасности.
3. Прожигание рабочего изделияМногие начинающие пользователи ведут резку вертикально вниз перпендикулярно рабочей поверхности (под углом 90°). Из-за этого расплавленный металл сдувается обратно в горелку. Более эффективный метод – наклонить металл под углом (60° по горизонтали, 30° по вертикали) и затем повернуть горелку вертикально. Таким образом расплавленный металл будет сдуваться в сторону от горелки.
4. Не прикасайтесь форсункой к рабочему изделиюНе касайтесь форсункой рабочей поверхности при силе тока более 45А. Это значительно сокращает срок службы форсунки, так как через нее проходит двойная дуга. Двойная дуга и повышенный износ также могут возникать, если перемещать горелку непосредственно по трафарету.
5. Новички должны пользоваться насадкой для контактной резкиМногие системы имеют изолированную насадку, которая защелкивается на форсунке. Благодаря ней горелку можно прислонить к изделию и плавно перемещать по поверхности, создавая ровный разрез.
6. Правильная скорость резкиПри правильной скорости резки поток расплавленного металла должен выходить с нижней стороны пластины под углом 15-20°. При слишком низкой скорости будет возникать окалина, которая представляет собой скопление расплавленного металла с нижней стороны разреза. Окалина также может возникать и при слишкой высокой скорости перемещения, потому что тогда у дуги не будет достаточно времени на полное проплавление металла. Другими словами, слишком большая или малая скорость приведет к падению качества резки. Окалину из-за низкой скорости резки можно узнать по простоте удаления. Обычно ее можно снять рукой, в то время как для удаления окалины, образующейся при слишкой высокой скорости резки, требуется шлифовка.
7. В начале работы увеличьте мощность на максимумСначала задайте максимальную мощность аппарата, а затем снизьте ее до наиболее эффективной. Чем выше мощность, тем обычно лучше, особенно при высокоточной резке или необходимости в небольшом разрезе.
8. Сократите длительность горения вспомогательной дугиИз-за повышенного износа деталей горелки необходимо максимально сократить время горения вспомогательной дуги. Для этого перед включением плазменную горелку нужно поместить непосредственно возле рабочего изделия.
9. Поддерживайте постоянное расстояние до рабочего изделияОптимальное расстояние между горелкой и рабочим изделием составляет 3-5 мм. Колебания горелки вверх и вниз только затруднят резку.
10. Ведите резку в наиболее подходящем направленииЕсли Вам нужно создать разрез в виде окружности и использовать внутреннюю круглую деталь, горелку необходимо перемещать по часовой стрелке. Если Вам нужна внешняя часть заготовки, из которой был вырезан круг, нужно перемещаться против часовой стрелки.
Так как Вы направляете горелку от себя, более высокое качество реза и более ровные края будут с правой стороны по направлению резки.
11. Наклоняйте горелку в направлении, противоположном направлению сваркиПри резке материалов большой толщины при приближении к последнему сегменту материала горелку можно немного повернуть, чтобы направить поток плазмы в направлении, противоположном направлению резки. Таким образом вначале будет прорезана нижняя часть детали и не образуется уголок, который обычно остается при резке пластин большой толщины. Последний сегмент разреза нельзя отламывать постукиванием горелки.
Подобрав подходящую модель для своей задачи и овладев некоторыми приемами профессиональной резки, Вы сможете выполнить любой проект. Помните, что плазменная резка обладает множеством преимуществ и позволяет наладить высокопроизводительную и качественную резку металла.
www.lincolnelectric.com
Принцип плазменной резки
Плазменная резка в Туле
Тульское предприятие ООО «УСТ Сибирь» располагает необходимыми мощностями высокотехнологичного и современного оборудования для плазменной резки.
- Плазменная резка листового металла производится оборудованием MultiCam серии 3000.
- Это оборудование обеспечивает обработку листов толщиной до 38 мм и размерами 6000 х 1500мм. При этом возможна качественная воздушная резка металла толщиной до 25мм.
- Оборудование обеспечит так же обработку нержавейки и черного сортамента.
- Мы выполняем заказы за максимально короткое время. На предприятии обеспечивается бесперебойная работа в несколько смен, а склады всегда полны необходимыми запасами.
- Технический контроль работ и изделий поставлен на серьезно высокий уровень, что полностью исключает появления брака. Работы ведутся в полном соответствии с заказом и чертежами заказчика. Готовые изделия тщательно зачищаются.
Преимущества и недостатки плазменной резки
А ниже приведены все известные преимущества и недостатки осуществления как плазменной резки, так и резки под водой. Принимать решение о выборе разновидности резки следует исходить из задач и специфических условий на предприятии.
Сухая плазменная резка:
Преимущества - Простые действия - Хорошая контролируемость процессом - Низкие затраты при повторяющихся процессах по сравнению с подводной резкой - Применение к металлическим листам, толщина которых более 40мм. - Скорость резки выше, чем под водой - Гибкость действий не ограничена размерами обрабатываемого материала.
Недостатки - Уровень шума при резке очень высок - Необходимы системы экстрагирования - Для защиты от ультрафиолетовых лучей нужны дополнительные устройства
Плазменная резка под водой:
Преимущества - Отсутствие пыли - Низкий уровень шума при резке - Необходимости в средствах защиты от ультрафиолетовых лучей нет - Обрабатываемые листы подвергаются меньшей деформации за счет охлаждения водой.
Недостатки - Увеличения риска коррозии после резки - Нельзя наблюдать за процессом резки - Во время резки менять параметры невозможно - Процесс удаления воды и обработка усложнены - Как правило, кромки обработанного материала получаются чуть шероховатыми - Существуют головки только для резки металла толщиной более 6мм.
Экономическая целесообразность
Плазменная резка требует сравнительно меньших финансовых затрат, чем лазерная. На рисунке ниже показаны расчеты затрат на осуществление резки одного метра материала лазерным, ацетиленокислородным и плазменным способами. В каждом случае резки использованы по одному режущему инструменту на установку. Расчеты достаточно реалистичны и отражают действительную разницу между резками.
Рис.1. Сравнительный анализ затрат на резку одного метра материала применительно к разным способам термической резки. X - толщина листа мм. Y- затраты евро/м. Синяя кривая - ацетиленокислородная резка. Малиновая кривая - лазерная резка. Красная кривая - плазменная прецизионная резка. Зеленая кривая - плазменная традиционная резка.
Не смотря на высоко технологичность, оборудование по лазерной резке требует особого подхода для обеспечения безопасности. Для этого целесообразно назначить обученного оператора, отвечающего за безопасную работу установки в целом. Сравнительно высокие материальные затраты на ацетиленокислородную резку объясняются низкой скоростью резки и возникновением необходимости дальнейшей обработки материала. Но эти расходы можно снизить с использованием нескольких резаков одновременно. Это позволит существенно сократить сумму вложений.
Ниже приведены данные по расходу на час работы устройств: для ацетиленокислородной резки с тремя головками, для плазменной резки (250 А) и для лазерной резки, мощность которого 2,5 кВт. Начальные расходы вложений на лазерное устройство взяты на 2,6 раз больше плазменного. В качестве материала выбран 12 миллиметровый лист марки S235JRG2.
Ацетиленокислородная установка с тремя головками: - Стоимость установки 160000 евро - Затраты 70,75 евро - Скорость резки 60 см/мин. - Стоимость резки одного метра 0,65 евро/мин.
Установка плазменной резки (250 А) кислород: - Стоимость установки 175000 евро - Затраты 78,85 евро - Скорость резки 200 см/мин. - Стоимость резки одного метра 0,65 евро/мин.
Установка лазерной резки мощность 2,5 кВт, кислород: - Стоимость установки 450000 евро - Затраты 143,75 евро - Скорость резки 90 см/мин. - Стоимость резки одного метра 2,66 евро/мин.
Как видно из приведенных выше данных, расходы для резки одного метра металла плазменным и ацетиленокислородным способами одинаковы. Расчеты сделаны с учетом усредненных показателей расходов на современных предприятиях, и могут быть изменчивы в зависимости от конкретных условий.
Таким образом, можно сделать вывод, что плазменная резка составляет заманчивую альтернативу двум другим способам с точки зрения экономической целесообразности.
Информация о плазменной резки металла
Плазменная резка металла представляет собой термический процесс, при которой применяется высококонцентрированная энергия. Это позволяет обеспечить высокую скорость резки низколегированных и мягких сталей, что экономически очень выгодно. Резка металла ацетиленокислородным способом требует сравнительно большего потребления энергии, чем резка металла плазмой, которая обеспечивает достаточно высокую точность обработанных деталей, ограничивая возможные неточности лишь мелкими деформациями и короблениями. Плазменная резка металла составляет конкуренцию с лазерным и ацетиленокислородным способами.На рисунке наглядно демонстрировано сравнение скоростей резки разных видов, в зависимости от толщины листового металла. Видно, что наиболее высокую скорость и качество резки обеспечивает плазменная резка листового металла. Следует отметить, что за последние годы резка металла плазменным способом подверглась значительным усовершенствованиям. Специалистам знаком такой термин, как «прецизионная плазменная резка металла». Он применяется при использовании дополнительной среды. До начала 90-х годов установки по плазменной резке под водой и с впрыскиванием воды считались наиболее экономичными и современными. Но последующие вскоре серьезные усовершенствования установок для сухой резки, привели к применению воздуха, затем и кислорода в качестве режущего газа. Были существенно увеличены и сроки службы электродов, и скорость резки. Сухая резка металла в новых установках является наиболее предпочтительной
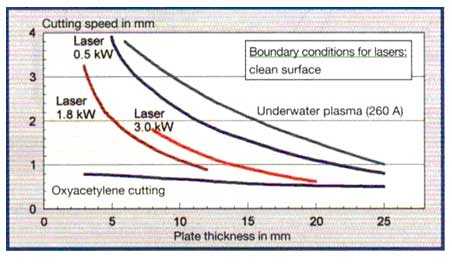
Рис.2. Сравнительные скорости резки: Y- скорость резки металла в мм. X - толщина листового металла в мм. Снизу вверх: 1-ацетиленокислородная резка. 2-лазер 1,8 кВт. 3- лазер 3,0 кВт. 4-лазер 0,5 кВт. 5 – резка металла плазмой под водой (260 А). 6 – Бортовые условия для лазеров: чистая поверхность.
Традиционная резка металла плазмой
Традиционная резка металла плазмой производится соплом, при подаче плазменного газа. Последний поступает в канавки, которые имеют V образный вид и вписанные углы от 60 до 100. Обычно резка происходит в атмосфере. Плазменная дуга возникает между катодом (неплавящимся электродом) и анодом – заготовкой. Между соплом и электродом дуга возникает редко. Такая плазменная дуга называется «непрямого действия». Как правило, этот процесс используют практически только вручную, и применяется к непроводящим материалам и тонким листам.
Плазменная резка металла с использованием дополнительной среды
Резка с использованием дополнительной среды – это следующий этап усовершенствования. Смысл в том, что эта среда ограничивает длину плазменной дуги. При использовании кислорода как режущего газа, параллельность обработанных поверхностей листа толщиной примерно 3мм сравнима с показателем лазерной резки с кислородом. Получение параллельных поверхностей возможно даже при резке листа 8мм-й толщины. С использованием азота, как режущего газа, можно получить очень гладкие, но слегка выпуклые обработанные поверхности. Применение резки с использованием дополнительной среды возможно не только в атмосфере – сухая резка, но также под водой. Если дополнительной средой является газ, то это просто сухая резка. В настоящее время этот способ находит широкое применение. Он наиболее популярен в предприятиях, где получают профильные поверхности практически любых размеров, ограниченные только параметрами ванны с водой. К тому же, вода между экранирующим соплом и плазмой может служить дополнительной средой. Воду, как дополнительную среду, принято использовать для резки алюминия и высоколегированной стали. Плазменная резка с впрыскиванием воды применима также для низколегированной и мягкой стали. Давление пара и образовавший при тангенциальном впрыскивании воды водяной колокол, исполняют роль дополнительных ограничителей плазменной дуги, точно так же, как при использовании дополнительного газа. Резку с впрыскиванием воды часто используют при работах под водой. Рис. 3 демонстрирует примеры применения газовых резаков в разных процессах.
Рис. 3. Схематичное представление применения плазменных резаков:а) обычный плазменный резак; b) резак с использованием дополнительного газа; с) плазменный резак с впрыскиванием воды: 1- электрод; 2 – сопло; 3 – охлаждающая среда; 4 – крышка сопла; 5 – плазменная дуга; 6 – плазменный газ; 7 – дополнительная среда; 8 – вода.
Использование воды или газа при резке листа с толщиной примерно 8мм, с двух сторон прорези образуются обработанные кромки, почти параллельные друг другу. Некоторые производители режут листы толщиной больше 8 мм – вплоть до 12мм. Если повернуть резак определенным образом, можно получить «хорошую и плохую сторону» и при прямых резах. Специальные резаки позволяют увеличить плотность тока за счет большего ограничения плазменной дуги вращением газа. Это так и рассматривают: резка с увеличенным ограничением. Принцип вращающего газа и применение резаков с многоступенчатыми возможностями при парциальном нагнетании газа показали, что это эффективно, когда производится резка толстого металла – толщиной до 30мм. При этом одна поверхность получается перпендикулярной другой, как и при лазерной резке, и для этого нет необходимости повернуть режущую головку
Используемые режущие газы для плазменной резки
Для плазменной резки низколегированных и мягких сталей самым подходящим в качестве режущего газа является кислород. Один из особенностей применения кислорода состоит в том, что расплавленное железо легко удалять из прорези, так как оно имеет меньшую вязкость. В итоге кромки обработанного материала получаются без заусенцев. Кислород еще и способствует тому, чтобы обработанные кромки не содержали повышенного азота.
Азот тоже выступает как режущий газ. В этом случае, при равной толщине металлического листа, резка производится с меньшей силой тока, благодаря чему уменьшается термическая нагрузка на электрод, увеличивая срок его службы. А с другой стороны резка толстого металла может производиться и в случае, когда нагрузка на электрод не уменьшается. Но скорее всего содержание азота в кромках обработанного металла может увеличиться. Это создаст трудности при дальнейшей обработке материала. В качестве плазменного газа, воздух самый дешевый. Но использование воздуха сопровождается с рядом недостатков. Срок службы электрода сокращается, а уровень азота на кромках повышается.
Более подробную информацию вы можете узнать позвонив по телефону 8 (4872) 33-03-92
sibir-corp.ru
Аппарат для плазменной резки и сварки предназначен для высокотемпературного местного нагрева плазменной струей поверхностей материалов малых толщин в процессах термической обработки.Области применения аппарата плазменной сварки и резки — плазменная резка электропроводных и не электропроводных материалов, пайка и пайко-сварка высокотемпературными припоями, сварка черных и цветных металлов (ремонт дисков, изделий из алюминиевых сплавов), поверхностная термообработка (местный отжиг, закалка, огневая зачистка) и другие работы, связанные с высокотемпературным местным нагревом.В плазменной горелке реализована технология получения плазмы из водяного пара. В общих чертах, устройство плазменной горелки можно описать следующим образом: в узком канале сопла горелки зажигается электрическая дуга, а водяной пар продувается через этот канал и интенсивно охлаждает дугу. При этом водяной пар ионизируется, и создается плазменная струя температурой 6000 градусов и более. Высокотемпературная дуга позволяет резать металл быстро и точно, причем процесс эффективен при работе с материалами разной толщины — от 0,5 до 50 мм. В отличие от кислородной резки плазменная технология позволяет разрезать как железосодержащие, так и не содержащие железа металлические материалы. Использование плазменной технологии для резки металлов, не содержащих железа, — это более быстрая, безопасная и эффективная альтернатива механической резке.Кроме того, в процессе резки плазмой не нагреваются обширные участки разрезаемого металла. Металл, разрезанный «плазменным резаком», охладится гораздо быстрее, чем металл, разрезанный кислородной резкой. Функционально роль пара рабочей жидкости сводится к охлаждению наиболее нагруженных частей горелки (сопла и катода), стабилизации столба дугового разряда и выдуванию дуги из сопла. Система подачи пара работает по «открытой схеме», то есть пар из резервуара самотеком по каналам охлаждения попадает в разрядную камеру и выбрасывается в атмосферу через сопло. Стабилизация дуги, то есть центрирование дуги относительно оси центрального отверстия сопла, обеспечивается за счет соосности катода и сопла специальной конструкции и спирального закручивания потока пара с помощью тангенциальной его подачи в разрядную камеру. Запас рабочей жидкости размещен в резервуаре горелки. Резервуар горелки заполнен капиллярно-пористым влаговпитывающим материалом, служащим для транспортировки рабочей жидкости при помощи капиллярного эффекта к поверхности нагревателя. Источник питания имеет отрицательный потенциал на катоде и положительный потенциал на сопле. Аппараты плазменной резки могут делиться на две категории: 1. Инверторные аппараты плазменной резки.К достоинствам их можно отнести такие параметры, как низкое энергопотребление, компактность, небольшой вес, красивый дизайн. Это значит что аппарат можно заказать в интернет-магазине, например можно инвертор купить в Ростове. К недостаткам - ограничение по максимальной мощности (как правило, не более 70 Ампер), невысокая ПВ (продолжительность включения) особенно на больших токах. Но основным недостатком, является то, что инверторные плазморезы очень чувствительны к перепадам напряжения.2. Трансформаторные источники плазменной резки.К достоинствам можно отнести высокую надежность, при падении напряжения не происходит поломки аппарата, только падает его мощность, высокое ПВ (продолжительность включения), в некоторых случаях достигает 100%, хотя для ручной плазменной резки вполне достаточно и 70%. Установки с ПВ выше 70% вполне можно использовать для автоматической резки с ЧПУ, где продолжительность непрерывной работы плазмотрона гораздо дольше, чем при ручной резке плазмой.К недостаткам можно отнести габариты и вес, значительно больший, чем у плазменных инверторов, более высокое энергопотребление.
Проплавление отверстий плазменной дугойПроплавить отверстие уже можно, когда угол наклона горелки составляет 40 градусов. Нажмите кнопку выключателя горелки плазменной резки. Когда загорится режущая дуга, наклоните горелку так, чтобы угол ее наклона составлял 90 градусов, и дуга насквозь проплавит основной металл. Лучше всего руководствоваться правилом, что таким способом можно проплавить металл, толщина которого не превышает наибольшей указываемой в паспорте аппарата толщины разрезаемого металла.
Скорость резкиПроверьте скорость резки аппарата. Обычно она измеряется сантиметрами в минуту. Некоторыми аппаратами металл толщиной 30 мм можно перерезать в течение 5 минут, другим - достаточно одной минуты.Скорость резки - очень важная характеристика, особенно при массовом производстве, когда необходимо уменьшать затраты времени. Входная мощностьПроверьте первичное напряжение и необходимую для источника питания силу тока. Также определитесь, необходим ли вам универсальный аппарат, который мог бы работать с различным напряжением и током. Некоторые аппараты могут использовать только напряжение 220 В или 380 В, однофазный или трехфазный ток питания.В некоторых аппаратах европейских производителей есть функция Auto-Line - это возможность подсоединения к любой электрической сети 50 Гц или 60 Гц, однофазной или трехфазной. Продолжительность работыЭто очень важная характеристика, на которую необходимо обратить внимание при покупке аппарата. Продолжительность работы - это время, в течение которого аппарат, не перегреваясь, может резать.Например: если продолжительность работы (ПН) аппарата 60 %, то аппарат без перерыва может работать 6 минут, а затем в течение оставшихся 4-х минут ему необходимо охлаждаться. Большая продолжительность работы очень важна, если требуется выполнять длинные разрезы, если требуется высокая производительность или если аппарат используется в обстановке при повышенной температуре. Соответствующая продолжительность работы обычно указывается для максимальной мощности аппарата в данном случае. Если аппарат будет использоваться с меньшей мощностью, то соответственно увеличится его продолжительность работы. Температура среды (в которой будет эксплуатироваться аппарат плазменной резки) также может иметь влияние на продолжительность работы. Плазменная горелка (плазматрон) Выбор плазматрона зависит от особенностей материалов или продуктов, которые требуется резать. Плазматрон всегда должен быть достаточной мощности, должен обеспечивать качественную резку в тяжелых рабочих условиях и при интенсивной эксплуатации быть стойким к ударам. Можно использовать плазматроны разной конструкции. Например, плазматрон с медным соплом которое более прочно, чем керамическое, практически не бьется, имеет воздушное охлаждение. Рукоятка может быть укомплектована крепящимся к плазматрону дополнительным элементом, который будет поддерживать наконечник на расстоянии от 1,6 мм до 3 мм от рабочей поверхности. Это облегчает работу оператора, так как можно двигать плазматрон на постоянном требуемом расстоянии от рабочей поверхности. Длина дополнительного элемента (фиксированное расстояние между рабочей поверхностью и плазматроном) зависит от толщины разрезаемого металла и требуемой силы тока. Используя при резке малые токи, можно соплом прикоснуться к поверхности металла или провести по металлу. При использовании для резки большого тока (выше 60 А) расстояние между горелкой и поверхностью металла должно быть 1,6-4,5 мм. При выборе плазматрона для плазменной резки необходимо определиться, для каких целей он будет использоваться, так как возможны различные конструкционные решения. Например, если горелка используется исключительно в диапазоне малых токов и может разрезать только тонкие листы металла, тогда для охлаждения плазматрона защитный газ не требуется, поэтому в этом случае в горелку подается только необходимый для резки воздух. Если плазматрон используется для резки толстых листов металла, то требуется больший ток, поэтому в плазматрон желательно подавать не воздух, а защитный газ (азот) для охлаждения плазматрона. При этом качество резки улучшается. МатериалыДля плазменной резки требуется не только сжатый воздух, но и другие комплектующие части и материалы. Это сопло горелки и электрод для резки. Изношенные или поврежденные сопла или электроды оказывают влияние на качество резки. Низкая квалификация оператора, влажность воздуха, резка толстых листов металла с использованием интенсивных режимов ускоряют износ данных комплектующих частей.Оптимальное качество резки достигается только при одновременной замене сопла и электрода.Вес и размерыЕсли требуется переносной аппарат плазменной резки, его вес и размеры являются очень важными факторами. Можно приобрести небольшие переносные аппараты, весящие менее 40 кг. Также существуют мощные аппараты плазменной резки, которые весят намного больше, они являются стационарными постами резки и позволяют выполнять качественную резку металлов толщиной до 50 мм. Как безопасно работать с оборудованием плазменной резкиВыполняя кузовной ремонт, работая с оборудованием плазменной резки необходимо жестко придерживаться правил техники безопасности, так как, выполняя плазменную резку, мы имеем большое количество представляющих опасность факторов: высокое напряжение, температура, ультрафиолетовое излучение и расплавленный металл. Необходимо носить одежду сварщика, иметь сварочный щиток со стеклами соответствующей степени затемнения.Перед началом резки осмотрите защитный щиток, сопло и электрод, не начинайте работу, если сопло или электрод недостаточно закреплены.Не стучите плазматроном, стараясь удалить брызги металла, так как можете его повредить. Если хотите экономить материалы, избегайте частого зажигания и обрыва плазменной дуги. Всегда руководствуйтесь "Инструкцией пользователя".Правильно эксплуатируя и обслуживая аппарат плазменной резки, вы сможете выполнять резку с высокой скоростью, качественно и чисто. |
autoevo.net
Плазменная резка - это... Что такое Плазменная резка?
Плазменная резка — вид плазменной обработки материалов резанием, при котором в качестве режущего инструмента вместо резца используется струя плазмы.
Между электродом и соплом аппарата, или между электродом и разрезаемым металлом зажигается электрическая дуга. В сопло подаётся газ под давлением в несколько атмосфер, превращаемый электрической дугой в струю плазмы с температурой от 5000 до 30000 градусов и скоростью от 500 до 1500 м/с. Толщина разрезаемого металла может доходить до 200 мм. Первоначальное зажигание дуги осуществляется высокочастотным импульсом или коротким замыканием между форсункой и разрезаемым металлом. Форсунки охлаждаются потоком газа (воздушное охлаждение) или жидкостным охлаждением. Воздушные форсунки как правило надежнее, форсунки с жидкостным охлаждением используются в установках большой мощности и дают лучшее качество обработки.
Используемые для получения плазменной струи газы делятся на активные (кислород, воздух) и неактивные (азот, аргон, водород, водяной пар). Активные газы в основном используются для резки чёрных металлов, а неактивные — цветных металлов и сплавов.
Преимущества плазменной резки:
- обрабатываются любые металлы — черные, цветные, тугоплавкие сплавы и т. д.
- скорость резания малых и средних толщин в несколько раз выше скорости газопламенной резки
- небольшой и локальный нагрев разрезаемой заготовки, исключающий ее тепловую деформацию
- высокая чистота и качество поверхности разреза
- безопасность процесса (нет необходимости в баллонах с сжатым кислородом, горючим газом и т. д.)
- возможна сложная фигурная вырезка
- отсутствие ограничений по геометрической форме.
Примечания
См. также
Ссылки
xzsad.academic.ru