Ржавый трос добавил на 3 стр. Как сделать нож из троса
Нож из троса своими руками
Приобрести нож из качественной стали, конечно, не проблема. Если не хватает ассортимента обычных или фирменных клинков, можно найти специалиста, работающего по индивидуальному заказу.
Однако можно пойти и другим путем – сделать нож самому. С первого раза выковать идеальный клинок, скорее всего, не получится, но кто знает…
А самодельный нож из троса – это стоящая затея, результатом может стать качественный клинок с видимым рисунком на лезвии, образованным перемешиванием слоев металла в процессе его ковки.
Выбор материала
Изготовлением клинков в наше время занимаются только истинные ценители этого ремесла. Однако даже начинающий кузнец и любой желающий может попробовать выковать самодельный нож.
Проще всего это сделать из куска толстой арматуры, старого напильника или отрезка автомобильной рессоры. Чуть сложнее будет расковать сверло или обойму подшипника. Можно получить интересный результат из сработанной цепи от бензопилы или двигателя автомобиля.
Еще одним материалом, который после ковки может стать качественным клинком, является трос. Его жилы состоят из углеродистой стали, способной хорошо держать острие после закалки. Если удастся сохранить плетеный рисунок после ковки, может получиться очень оригинальный клинок, отдаленно напоминающий дикую дамасскую сталь.
Что нужно знать, чтобы выяснить, как сделать нож из троса? Два важных нюанса: первый – сохранятся ли свойства высокоуглеродистого материала в процессе обработки; второй – проявится ли на лезвии видимый рисунок, изящно переходящий в отточенное острие.
Дамасская сталь
Раньше острые, пластичные и надежные клинки с узорчатым рисунком на лезвии называли булатными (по одной из версий – от провинции Фулад в Персии, где их изготавливали). Достигались такие характеристики и видимый эффект различными методами.
Сталь можно было выплавить в тигле путем металлургического литья, экспериментируя с составом материала. Другой вариант – «сварить» разные по твердости стальные полосы в кузнечном горне и затем расковать полученную заготовку. Клинки, выкованные кузнецами по специальной методике, стали называть дамасскими.
Отличаются они именно методом изготовления и технологией, а не характеристиками и степенью выраженности рисунка. Расковав нож из троса, своими руками можно попытаться создать клинок, отдаленно напоминающий такой материал. И хотя рисунок на лезвии – это не самоцель, он все-таки является отличительной особенностью дамасской стали.
Кузнечный инструмент и материалы
Чтобы выковать нож из троса своими руками, нужно освоить хотя бы на минимальном уровне ремесло кузнеца. Для этого понадобится пара молотков: один массивный (до 2 кг), другой – легче (до 0,5 кг) для тонкой работы, клещи, наковальня и самодельная печь (кузнечное горнило) с принудительной подачей воздуха.
Не обойтись в процессе изготовления без болгарки, точильного станка, электросварки. Понадобятся тиски и разводной ключ. Топливом для горнила может служить древесный уголь из пород, дающих большой жар, ведь разогревать заготовку придется до температуры свыше 1200 °С.
Для лучшего «сваривания» можно использовать буру в качестве флюса. Она убирает окалину и препятствует выгоранию углерода из материала. Также необходимо подготовить масло для закалки, обеспечить технику безопасности.
Возможность воспользоваться чьей-то кузнечной мастерской или кузней предприятия с механическим молотом существенно облегчит задачу.
Подготовительные операции
Чтобы изготовить нож из троса, прежде всего нужно сделать на бумаге его набросок или эскиз. Затем придется найти подходящий материал. Нужно проверить его и хотя бы отдаленно определить в нем состав углерода.
От этого зависит, возьмет ли будущий клинок закалку, будет ли он держать острие и получится ли провести кузнечную «сварку». Проверку производят на искры от точильного камня. Умеренно плотный оранжевый их сноп будет означать, что сварка возможна, углерода в стали содержится около 1%, чего достаточно для закалки.
Далее нужно отрезать кусок троса необходимой длины. На этом этапе определяются со способом изготовления рукояти. Она может быть из цельного отрезка троса без проковки. Нож будет оригинально смотреться, но иметь приличный вес.
Другой вариант – приварить электросваркой к отрезку троса прут арматуры. За такую ручку удобно держаться, нагревая заготовку в горниле и обрабатывая ее молотками. На ней потом можно сделать наборную рукоять или, расклепав, установить декоративные накладки.
Перед началом работы трос стягивают хомутами из стальной проволоки в нескольких местах. Это делается для того, чтобы в процессе нагрева тонкие жилы не расплетались.
Как из троса выковать нож?
В разожженное горнило закладывают заготовку и дают ей разогреться до 800 °C. На этом этапе жилы троса отпускаются (отжиг), материал становится податливым. Дополнительно выгорает масло и грязь.
После остывания заготовка зажимается в тиски и электросваркой обваривается один из концов троса. Разводным ключом он «докручивается» по ходу плетения до максимальной плотности. Обваривается другой край с одновременным креплением отрезка арматуры для удобства работы.
Заготовка постоянно разогревается. Чем чаще это делать, чем интенсивнее происходит ковка, тем лучше «сваривается» материал. После грубой обработки переходят к проковке лезвия, будущей режущей кромки, хвостовика. На этом этапе больше используют молоток меньшей массы, придавая заготовке очертания, напоминающие эскиз будущего клинка.
Сложности технологии
Необходимо постоянно следить за температурой заготовки, не давая ей остывать. Работая тяжелым молотом, особенно без должной практики и опыта, можно легко повредить завитки троса в местах, где должен остаться отчетливый рисунок плетения. Нежелательные попадания ребром или углом кувалды по разогретой заготовке оставляют глубокие вмятины, которые не всегда удается сточить.
Особый подход
Ковка ножа из троса возможна и по другой технологии. Есть мастера, которые перед кузнечной «сваркой» упаковывают отожженную и уплотненную заготовку троса необходимой длины в отрезок трубы из нержавеющей стали. Ее диаметр подбирается таким образом, чтобы трос входил в нее очень плотно, с некоторым усилием.
Оба конца такого футляра заваривают электросваркой, сплавляя концы троса с трубой. Заготовка разогревается до температуры 1200-1300 °C и в таком виде расковывается. Легированная нержавеющая сталь трубы с тросом не сваривается, а служит только защитным чехлом от неравномерной ковки. Кроме того, раскаленный трос не вступает в контакт с кислородом воздуха и углерод в нем при ковке выгорает минимально.
Если использовать при этом гидравлический пресс, то можно существенно облегчить кузнечную «сварку». После нагрева до 1300 °C футляр с тросом внутри помещается под нагрузку и оставляется до остывания. Если использовать матрицы, то сразу можно сформировать утолщения под шейку для перехода с клинка на рукоять и обушок хвостовика. При следующем нагреве проковкой через футляр дорабатывается форма лезвия.
После остывания труба срезается на наждаке с торца, где будет острие. Футляр осторожно раскрывается с помощью зубила. Дальнейшая обработка заготовки происходит на наждачном круге. Предварительно обрезают лишние участки, делают спуски лезвия без окончательной заточки.
Термообработка
Закалка клинка так же важна, как и выбор стали. По технологии нож из троса после ковки имеет напряжение, его необходимо снять. Для этого заготовку нагревают до 800 °C и дают ей остыть.
Закалка производится при разогреве клинка до 1200 °C. Его опускают острием вниз в разогретое масло и держат неподвижно. Клинок после этого необходимо отпустить. Его очищают от нагара, нагревают до 200 °C и снова опускают в масло.
Травление и отделочные работы
После термообработки нож из троса шлифуется, производится окончательная доводка лезвия клинка и хвостовика для крепления рукояти. Для проявления рисунка заготовку опускают в раствор (5 %) хлорного железа и оставляют для травления. Время обработки зависит от желаемого эффекта и может составлять до одного часа.
Если перед этим на лезвие наклеить трафарет, на которой будет вырезан логотип изготовителя (инициалы или любой рисунок), в результате он отпечатается на стали и будет свидетельствовать об авторстве клинка. После этого производится тонкая шлифовка мелкозернистой наждачной бумагой и полировка лезвия.
До этой операции или уже после производится монтаж выбранного типа рукояти. Это могут быть накладки из ценных пород древесины с интересной текстурой, наборные шайбы различного материла в любой последовательности или, к примеру, отрезок рога оленя.
Такой оригинальный и мастерски выполненный нож из троса (фото сверху) с первого раза изготовить, может, и не получится, но если есть желание осваивать ремесло изготовления клинков, к такому результату нужно стремиться.
fb.ru
Как сделать кованый нож из стального троса
В поисках идеи изготовления совершенных инструментов мастера пробуют использовать самые необычные материалы и подручные средства. Кузнец реализовал одну из таких находок самоделкиных. Он показал, как изготовить свой кованый нож из металлического троса без эскизов. Если делать по заранее подготовленным чертежам и рисункам, продумывая всё до мелочей, так делают мастера, которые специализируются на изготовлении ножей.
В двух видеороликах канала «Kovko Kova4» показана технология изготовления ножа из такого прочного стального материала, как трос. Первое видео — сварка троса. Второе о поковке ножа.
Чтобы сварить трос и изготовить из него поковку для ножа, нужно сначала подготовить материал. В центре стальных витков находится веревка, нужно убрать, она мешает. Для этого придется витки частично расплести. На место веревки устанавливается проволока катанка 8 миллиметров.
Для подготовки к сварке готовим 2 обрезка. Завариваем края электросваркой. Затем укладываем вместе и снова соединяем сваркой. Прицепляем также ручку, за которую удобно держать. Посередине между трассами с обоих сторон были приварены 2 обрезка проволоки 8 миллиметров. Больше мастер ничего не делал дополнительного. Флюс — бура. Обсыпал нагретую заготовку. И снова в огонь. Всё остальное смотрите на видео.
Заготовка из сваренного троса. Показаны размеры. Если порезать поковку на три равные части, зачистить и собрать заново, можно снова сварить её. Как можно сделать несколько раз, меняя расположение обрезков. Сам мастер не задавался такой целью, а просто хотел сделать нож из троса. Поэтому заготовку разделил на две части. Из них получатся 2 ножа. На срезе поковок заметил какие-то темные пятна. Скорее всего это норма при сварке троса.
Здесь показано, каких размеров стало заготовка после ковки на молоте. Перед этим щеткой снимаем окалину. Трещин и пор не замечено. Из неё будет изготовлена поковка для ножа. Будут сформированы лезвие и ручка. Будут изготовлены спуски на режущей части. Остальную работу по доводке ножа нужно делать на точилах и гриндерах.
Покупка ножа из троса практически готова. Но по желанию ее можно еще укоротить. Саму длину лезвия. Кузнец оставил всё как есть. Ручка будет из двух накладок. Крепление на трех заклепках. Проделаны соответственно три отверстия. На самом лезвии появилась видимая глазу темная полоска. На острие замечена небольшая пара. Но при обработке это всё должно сточиться. В целом изделие из троса получилось хорошее.
izobreteniya.net
Ковка ножа своими руками | Строительный портал

Сегодня, даже при таком большом ассортименте различных ножей прекрасного качества от известных производителей, ножи ручной ковки по-прежнему пользуются особой популярностью. Это и неудивительно, так как такие ножи обладают особой энергетикой и привлекательностью. А если сам клинок сделан из легированной стали и со знанием дела, то такой нож бесценен. Из различных способов собственноручного изготовления ножа наиболее трудоемким является ковка ножа своими руками. Следует отметить тот факт, что ковка ножа позволяет создать наиболее прочный и качественный клинок, который прослужит не один десяток лет и при этом сохранит свои качества. Ковка ножа своими руками – дело, требующее от мастера высокого уровня навыков владения инструментом, знания металлов и их свойств. Для тех, кто решил выковать нож впервые, описанные ниже рекомендации помогут сделать свой первый клинок.
- Как выбрать сталь для ножа
- Инструмент для ковки ножа
- Конструкция ножа
- Ковка ножа из сверла
- Ковка ножа из подшипника
- Ковка ножа из рессоры
- Ковка ножа из напильника
- Ковка ножа из троса
- Закалка и отпуск клинка
Как выбрать сталь для ножа
Качественный самодельный нож отличает правильный подбор стали для него, от этого будут зависеть режущие и прочностные характеристики самого ножа. Чтобы правильно подобрать сталь, необходимо знать и понимать, какими свойствами обладает сама сталь. Для ковки ножа своими руками нужно ориентироваться на пять основных свойств стали – устойчивость к износу, твердость, прочность, вязкость, красностойкость.
Твердость – это свойство стали, указывающее на её способность сопротивляться проникновению в неё другого более твердого материала. Говоря проще, твердая сталь лучше сопротивляется деформации. Сам показатель твердости измеряется по шкале Роквела и имеет показатель от 20 до 67 HRC.
Устойчивость к износу – сопротивление материала изнашиванию в процессе эксплуатации. Это свойство напрямую зависит от твердости самой стали.
Прочность указывает на способность сохранять целостность под воздействием различных внешних сил. Проверить прочность можно на изгиб или при сильном ударе.
Пластичность – способность стали поглощать и рассеивать кинетическую энергию во время удара и деформации.
Красностойкость – это показатель, отвечающий за устойчивость стали к температурам и сохранению её изначальных качеств при нагреве. От того насколько сталь устойчива к термообработке, зависит минимальный показатель температуры, при котором её можно ковать. Самыми красностойкими сталями являются твердые марки, рабочая температура ковки для которых более 900 °C. При этом необходимо отметить, что температура плавления стали составляет 1450 – 1520 °C.
Все эти свойства связаны между собой и преобладание одного из них ведет к ухудшению другого. При этом то или иное свойство стали зависит от содержания в ней различных легирующих элементов и добавок, таких как кремний, углерод, хром, ванадий, вольфрам, кобальт, никель, молибден.
Наличие тех или иных легирующих элементов и их пропорциональное использование при изготовлении стали, знание свойств, которые придают легирующие элементы и добавки, позволило создавать сталь для определенных целей и нужд. Такие стали имеют каждая свою маркировку. При этом отечественные и зарубежные марки стали обозначаются по-разному. Для удобства в марке стали указан основной состав одного или нескольких легирующих элементов. Например, сталь марки У9 говорит о содержании в ней углерода в десятых долях процента. Аналогом стали марки «У» являются стали 10хх, где «хх» - это содержание углерода. И чем меньше значение, тем меньше его содержание. Или такая сталь как Х12МФ указывает на высокое содержание хрома и молибдена, что говорит о нержавеющих и высокопрочностных свойствах стали.
К отечественным маркам, которые часто используются при ковке ножей в домашних условиях, относятся все стали с маркировкой от У7 до У16, ШХ15, 65Г, Р6М5, Х12МФ. Из зарубежных аналогов можно выделить сталь O-1, 1095, 52100, M-2, A-2, 440C, AUS, ATS-34, D-2. Каждая их вышеприведенных марок используется в изготовлении ножей, различного инструмента и запчастей. Например, марки стали Р6М5, У7-У13, 65Г применяют для производства сверел, буров, тросов, рессор, подшипников, напильников. Поэтому именно из этих предметов народные умельцы делают ножи ручной ковки.
Конечно, можно найти и другие изделия из той или иной стали. Для этого достаточно будет прочитать полное описание марки стали и её применение в Марочнике Стали и Сплавов, а потом использовать изделие из неё для ковки ножа.
Инструмент для ковки ножа
Для ковки ножа потребуется определенный инструмент кузнеца, который можно приобрести в магазине. Но можно использовать и непрофессиональный инструмент:
- молот на 3 – 4 кг и молоток меньшего веса до 1 кг;
- кузнеческие щипцы или обычные пассатижи, но без изоляции на ручках, а также разводной ключ;
- тиски;
- наковальня или её самодельный аналог из двутавра;
- болгарка и сварочный аппарат;
- точильный станок;
- печь.
Если с обычным инструментом все более-менее понятно, то по поводу печи необходимо сделать некоторые пояснения. Все дело в том, что в обычном очаге сложно получить температуру более 900 °С. Да и греться заготовка там будет целую вечность. Поэтому необходимо немного усовершенствовать очаг. Если ранее Вы не занимались хотя бы закалкой металла, то придется сделать с нуля небольшую печь из толстостенного металла. Затем присоединить к ней трубу, по которой будет поступать воздух при помощи вентилятора или старого пылесоса. Таким нехитрым образом можно получить достаточно надежное горнило для доведения заготовок до температуры 900 – 1200 °С. В качестве топлива используется обычный древесный уголь, желательно такой, который дает как можно больше жару и горит подольше.
Конструкция ножа
Прежде чем приступить к самим работам, необходимо сделать эскиз самого ножа.
По сути, нож довольно простой предмет, состоящий из клинка и рукоятки. Но вот каждый из этих элементов имеет целый набор составляющих. На демонстрирующем конструкцию ножа фото можно увидеть все элементы ножа и как они называются.
Также необходимо знать и о некоторых основных профилях клинков, чтобы сделать наиболее подходящий эскиз. На фото ниже приведены профили ножей.
Выбрав наиболее подходящий для Вас профиль, можно смело приниматься за создание эскиза. Конечно, опытные мастера обходятся без зарисовки, но для новичка все же важно сделать эскиз и держать его перед глазами в процессе ковки.
Ковка ножа из сверла
Сверла получили большую популярность при ковке ножей благодаря используемой в них легированной стали Р6М5, которая отличается прочностью, легкостью заточки и износоустойчивостью.
При выборе сверла для ковки следует отметить один важный момент. Большие сверла состоят из рабочей спиралевидной части из Р6М5 и хвостовика из обычной стали. Маленькие сверла обычно полностью из Р6М5. При ковке ножа из большого сверла необходимо сразу определить, где какая сталь и где между ними граница. Сделать это можно достаточно просто, всего лишь немного проточив сверло по всей длине. Там, где обычная сталь, сноп искр будет большой и желто-оранжевого оттенка. А вот там, где легированная сталь, сноп будет реденьким и ближе к красноватому оттенку. Описанная выше процедура необходима для того, чтобы определить, где у ножа будет начинаться клинок, а где хвостовик. Закончив с этим, переходим к самой ковке.
Вначале разводим огонь в печи, подключаем поддув и ждем, когда угли разгорятся достаточно сильно, после чего помещаем сверло в горнило. Но делаем это с помощью клещей и так, чтобы хвостовик большей частью оставался вне огня.
Важно! Выполняя ковку ножа впервые, можно не сразу определить, когда металл нагрелся до необходимой температуры. Вследствие чего можно испортить не одно сверло. Поэтому прежде чем браться за ковку сверла, можно немного потренироваться с нагревом и ковкой металла на обычной арматуре. При этом необходимо запоминать, какого цвета был металл и когда он ковался наиболее мягко. Также стоит помнить о том, что на солнечном свете даже нагретый до 1100 °С металл будет выглядеть темным.
Как только сверло нагреется до необходимой температуры, а это более 1000 °С, его сразу же необходимо вынуть из горнила, и зажать низ хвостовика в тисках. После чего взять разводной ключ, зажать им верхушку сверла и сделать круговое движение, расправляя спираль. Делать все необходимо быстро, чтобы металл не успел остыть, иначе рискуете сломать сверло. Если не получилось сделать это за один раз, ничего страшного. Просто повторно раскалите сверло и повторите процедуру. В результате должна получиться относительно ровная полоска металла.
Следующим шагом будет ковка сверла и раскатка металла до приемлемой толщины. Тут все довольно просто. Раскалив металл до необходимой температуры, берем тяжелый молот и начинаем сильными, но равномерными ударами ровнять металл и придавать ему ровную форму. В результате должна получиться полоска металла толщиной около 4 – 5 мм.
Важно! При ковке металла необходимо постоянно следить за цветом заготовки. Как только она начала тускнеть, приобретая вишневый цвет, её сразу же возвращаем в горн. Лучше лишний раз накалить металл, чем сломать его под ударом молота.
Далее выковывается острие ножа. Тут все несколько сложнее. Дело в том, что необходимо придать заокругленную форму и при этом сохранить необходимую толщину лезвия. Вся работа практически ювелирная и потребует определенной ловкости. Ковка выполняется таким образом, чтобы постепенно заокругливая острие, понемногу оттягивалось лезвие в длину. Удары должны быть сильные, но аккуратные. У новичка может не получиться с первого раза, но немного практики все исправит.
Следующим шагом будет проковка режущей кромки ножа. Это довольно важный и сложный этап. Для этого потребуется более легкий молот и желательно с заокругленным бойком. Начиная с середины лезвия, постепенно сдвигаем металл вниз к режущей кромке. Стараемся сделать режущую кромку как можно тоньше. При этом следим, чтобы само лезвие оставалось прямым и ровным. Удары наносим очень аккуратно и стараемся прилагать лишь столько усилий, сколько требуется для небольшой деформации раскаленного металла. Помним о цвете заготовки и при необходимости отправляем её обратно в горнило.
После того как удалось выковать лезвие и острие, переходим к проковке хвостовика. Сами работы будут намного проще, чем при выковке лезвия. Вначале накаливаем круглый хвостовик сверла и затем раскатываем его сильными ударами молота. В зависимости от эскиза хвостовик может быть как узким, так и широким. Тут уже кому как нравится делать ручку ножа. Кто-то делает простые накладки, а кто-то делает наборную рукоятку.
По завершению ковки даем металлу постепенно остыть и затем переходим к шлифовке. На шлифовальном станке снимаем лишние слои металла и неровности, делая нож идеально ровным и блестящим. При шлифовке может уйти до 2 мм толщины, и нож станет намного легче и тоньше. Также на этом этапе можно выполнить заточку ножа. Напоследок выполняем закалку ножа. О том, как это делается, будет написано ниже.
Ковка ножа из сверла видео-обзор:
Ковка ножа из подшипника
Еще одним популярным материалом для ковки ножей является подшипник, а именно его внутренний или внешний обод. Причем внутренний даже предпочтительней. Все работы по ковке ножа из подшипника практически идентичны ковке из сверла. За некоторым исключением.
Во-первых, заготовку из ободка подшипника вырезаем при помощи болгарки. Длину стараемся взять с запасом, так чтобы и на нож хватило и еще 1 – 2 см осталось. Во-вторых, на начальной стадии ковки вырезанную заготовку следует приварить к прутку арматуры. И в таком виде накалять и ковать. В-третьих, если в случае со сверлом заготовку раскатывали из круглой в плоскую, то для обоймы подшипника её необходимо просто выровнять. А дальнейшие действия по ковке самого клинка и хвостовика полностью аналогичны. Единственное, что стоит отметить, – из подшипника все же удобнее делать нож с накладными рукоятками.
Ковка ножа из подшипника видео-обзор:
Ковка ножа из рессоры
В поисках подходящей стали для качественного ножа многие используют рессору. Металл этой автомобильной запчасти отличается высокой упругостью и долговечностью, что делает его прекрасным образцом для ножей ручной ковки. Справедливости ради, необходимо отметить, что нож из рессоры можно изготовить и обычным вырезанием профиля ножа с дальнейшей заточкой и закалкой. Но все же, чтобы нож был действительно надежным, его лучше проковать, тем более что толщина рессоры достаточно велика, а для хорошего ножа её следует уменьшить.
Ковку ножа из рессоры начинаем с зачистки болгаркой от ржавчины и разметки пластины. Потребуется лишь небольшая часть рессоры, поэтому отметив её, отрезаем при помощи болгарки. Далее привариваем заготовку к арматуре и накаляем её. После чего постепенно проковываем, доводя до необходимой толщины. Выковываем острие и режущую кромку, как это делать, описано выше на примере ковки ножа из сверла. Добившись желаемого, оставляем нож постепенно остывать и затем шлифуем и затачиваем его.
Ковка ножа из рессоры видео-обзор:
Ковка ножа из напильника
Износостойкую и прочную сталь можно найти в различном слесарном инструменте и напильник тому яркий пример. Изготовление ножей из напильника достаточно популярное занятие. Тем более что клинки получаются на редкость долговечными с прекрасной режущей кромкой. Но ковка ножа из напильника имеет свои особенности.
Прежде всего, потребуется очистить напильник от насечек и возможной ржавчины. Сделать это можно с помощью болгарки. Далее при необходимости отрезаем от напильника заготовку необходимой длины. После чего привариваем её к куску арматуры и засовываем в горнило. Накалив заготовку до нужной температуры, приступаем к раскатке заготовки до необходимой нам толщины. Затем делаем острие и режущую кромку. Хвостовик ножа из напильника лучше всего сделать под накладную ручку.
Ковка ножа из напильника видео-обзор:
Ковка ножа из троса
Изготовление ножа из стального троса довольно редкое явление. Так как в отличие от всех описанных выше заготовок, трос представляет собой разрозненные волокна проволоки, и ковать их довольно сложно. К тому же сталь троса не обладает такими высокими характеристиками, как сталь сверла или напильника. В большинстве своем ножи из троса куют из-за их необычного рисунка на клине, отдаленно напоминающего дамасскую сталь. Для того чтобы сделать такой нож, необходимо приложить несколько больше усилий, чем при ковке из обычного бруска стали.
Ковка ножа из троса начинается, как и обычная ковка. Вот только есть несколько маленьких секретов. Во-первых, это касается хвостовика. Многие мастера делают хвостовик ножа из троса в виде готовой рукоятки. Смотрится это весьма необычно и красиво. И тут есть два подхода в изготовлении рукоятки. Взять толстый трос и затем сварить его конец, сделав монолитным куском. Или сделать рукоятку в форме петли, а из концов выковать клинок. Во-вторых, ковка троса – дело сложное из-за разрозненных проволок, из которых состоит трос. Чтобы сделать нож, потребуется их сварить между собой. А это целое искусство и рассчитывать, что нож из троса получится с первого раза, не стоит. Сварку можно выполнить двумя путями. Первый – проварить электросваркой вдоль больших канавок. Второй – выполнить кузнеческую сварку. Второй вариант сложнее и в то же время предпочтительней.
Итак, выбрав способ создания рукоятки, приступаем к ковке ножа. Для этого раскаливаем трос до ярко-красного цвета. Затем вынимаем его и посыпаем бурой. После чего вновь отправляем в горнило. Таким нехитрым образом выполняется подготовка к кузнеческой сварке. Бура представляет собой соль тетраборной кислоты и применяется мастерами для сварки отдельных слоев стали. По сути это флюс, который облегчает процесс плавки и предохраняет расплавленный металл от попадания кислорода и устраняет оксиды металла. Буру можно найти в свободном доступе без особых проблем.
После того как трос обработали бурой со всех сторон и он раскалился от 900 до 1200°С и более, вынимаем его из горнила и начинаем проковывать. Удары наносим тяжелым молотом, но при этом стараемся сохранить волокна троса вместе. Сложность ковки троса именно в этом. Но потренировавшись можно добиться приемлемых результатов. В конце концов, трос можно накалять и проковывать сколько угодно раз. Но при этом каждый раз, нагревая его в горне, посыпать трос бурой. В результате получится монолитный кусок стали, состоящий из множества слоев, почти как у дамасской стали. После чего остается лишь выковать клинок необходимой формы. На демонстрирующих ковку ножей видео уже не раз было показано, как именно делается раскатка клинка, создание режущей кромки и острия.
Закалка и отпуск клинка
Как уже отмечалось ранее, закалка ножа – это один из самых важных этапов его изготовления. Ведь именно от того насколько правильно была она выполнена, зависят рабочие характеристики ножа. Сам процесс закалки выполняется уже после того, как нож остыл и был отшлифован на точильном станке.
Закалка клинка начинается с его нагрева от светло-красного до оранжевого цвета. После чего нож опускается в воду или масло. При этом в воду добавляется 2 – 3 ложки поваренной соли на 1 л, а температура воды должна быть 18 – 25 °С, масла 25 – 30 °С. Закалка выполняется довольно быстро и чтобы все прошло удачно после закалки клинок необходимо отпустить. Сама закалка стали происходит в диапазоне температур от 750 до 550 °С. Момент закалки можно даже прочувствовать, когда сталь начинает «дрожать и стонать» в жидкости. Как только процесс заканчивается, клинок необходимо достать и дать ему остыть естественный образом.
Отпуск клинка выполняется уже после закалки. Сам процесс подразумевает ослабление внутреннего напряжения стали, что делает его более гибким и устойчивым к различного рода нагрузкам. Перед тем как сделать отпуск, клинок следует очистить от возможной окалины и затем вновь нагреть. Но температура при отпуске значительно меньше. Сам нож нужно уже держать над пламенем и наблюдать за ним. Как только вся поверхность покроется желто-оранжевой пленкой, убираем нож от огня и даем ему остыть естественным образом.
Иногда закалка и отпуск производятся при помощи масла или воды, а иногда через масло в воду. Такая закалка выполняется очень быстро. Сначала клинок опускается в масло на 2 – 3 секунды, а затем в воду. При таком подходе риск сделать закалку неправильно минимален.
Ковка ножа своими руками лишь кажется простой задачей. Кроме того что придется довольно много помахать кузнечным молотом, так еще и без опыта в вопросе ковки металла с первого раза может не получиться выковать нож. Поэтому сначала необходимо набить руку и немного потренироваться, а затем уже приступать к ковке ножа.
strport.ru
Ковка ножа из троса | Судовой журнал Акселя (Axl's Logbook)
Ковка ножа из стального троса с режущей кромкой из У10 Forging blade from steel cable with cutting edge from the steel U10
Пишу опять-таки задним числом, но как бы в реальном времени о событии годовой давности - моей третьей в жизни ковке 3.08.2014, на которой я делал фоторепортаж по ковке ножа из троса.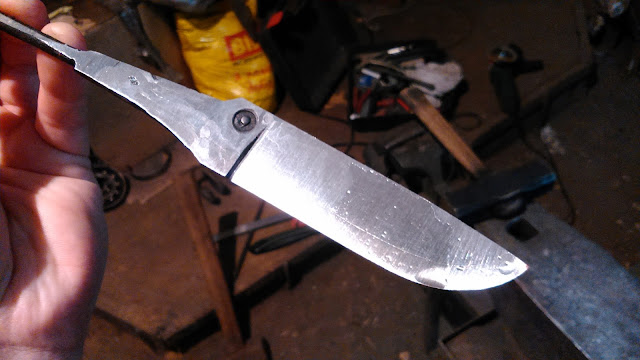
В кузне был помимо нас мрачный мужик, который, орудуя попеременно сварочным аппаратом и болгаркой, ваял замысловатые секции оград с художественными элементами. Потом правда выяснилось, что он вовсе и не мрачный, а очень даже общительный - просто амплуа такое:)
Мы сперва попили чаю, а потом Илья включил газовый горн и показал мне что и как устроено у него в кузне. Я довел на горячую до ума двое клещей - тех, что сковал у Виленыча, а также раскатал один немецкий подшипник - будет заготовка на клиночек, а то и на два.
Газовый горн - это конечно пипец как технологично: даже попить отойти нет времени - поковка моментально раскаляется... Да и остывает все очень медленно - это вам не на свежем воздухе ковать - практически промышленные условия!
Илья провел мастер-класс по ковке ножа из троса. Внизу подробно все изложено в виде фоток с пояснениями. К этому выкованному телу клинка в дальнейшем была приварена в торец (имеется в виду конечно же кузнечная диффузионная сварка) режущая кромка из стали У10. Этот момент я не застал, к сожалению (происходило сие в другой день). Впрочем, и процесс изготовления тела клинка весьма интересен и имеет свои нюансы. А как приварить РК Илюха мне еще покажет, а я уж это дело зафотофиксирую. До сих пор те, кому очень надо, могут посмотреть на ютубе - там примеров диффузионной сварки предостаточно.
Мастерская у Ильи. На переднем плане (как и положено звезде такого ранга) красуется лисонька-красавица-наковальня - однорогая, 75 кг.
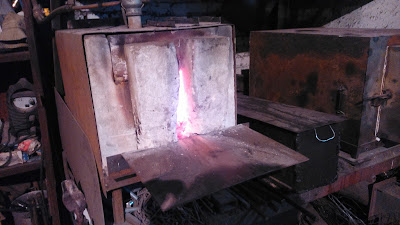
Горн на газе.
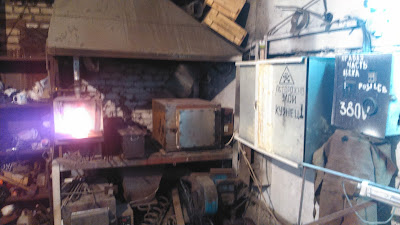
Горн, емкость с маслом и печка для отпуска и запекания тортиков из мокуме гане.
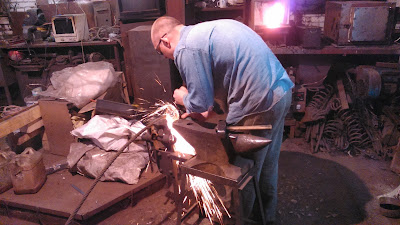
Илья отрезает стальной трос
болгаркой. Из сего троса и будет коваться тело будущего клинка
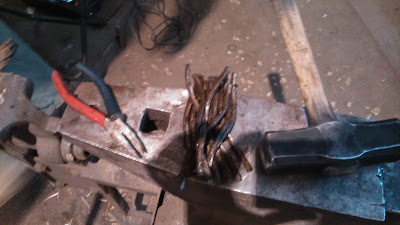
Стальной трос разобрали на мелких "червей" - все они грязные и в смазке, которую надобно отжечь.
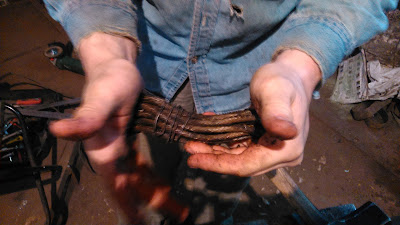
Из "червей" связали вот такую колбаску.
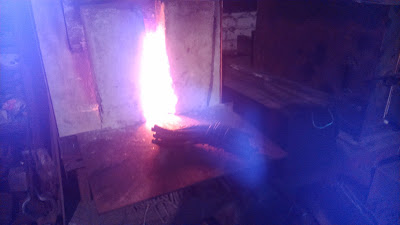
В топку ее!!!
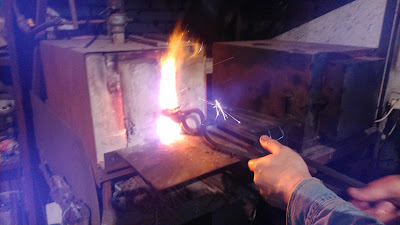
Отгорает смазка с троса - полыхает будь здоров!
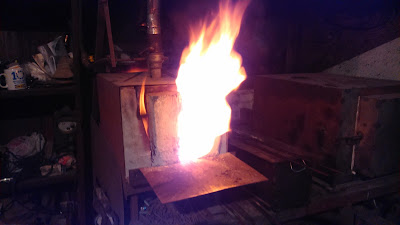

Раскаленные "черви" негодуют!
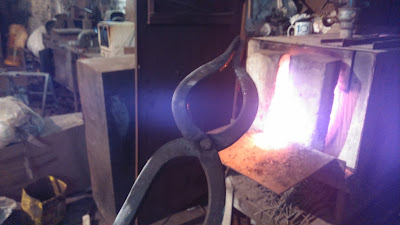
Клещи у Ильи несколько другой конструкции, нежели мои, самолично
откованные по заветам Виленыча с Ганзы.
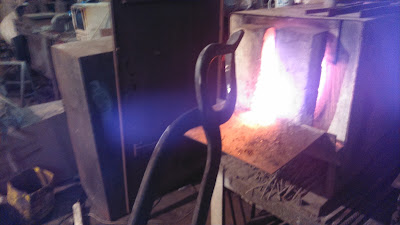
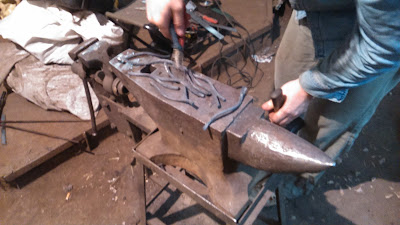
Устраиваем обожженным червям допрос с пристрастием.
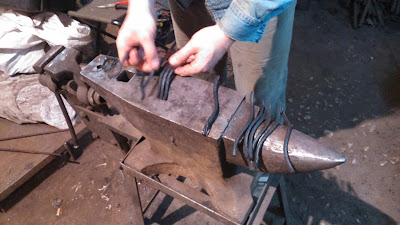
Формируем из них пакет.
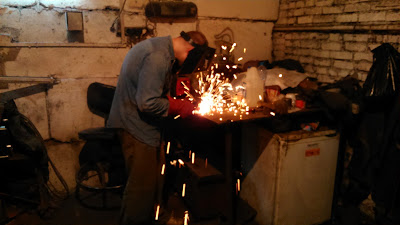
Хорошенько свариваем его.
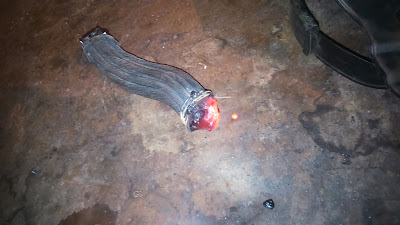
Подпалили червям задницу!
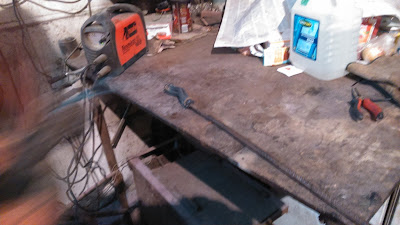
Теперь к пакету привариваем рукоятку из арматуры - с ней удобнее будет ковать,
держась за нее, нежели клещами цеплять.
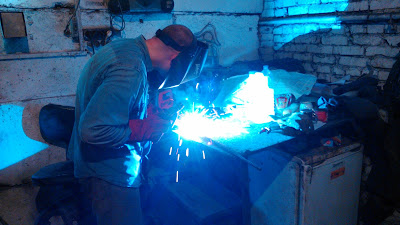
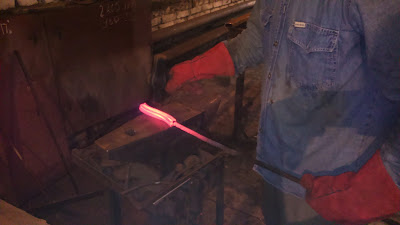
Другое дело!
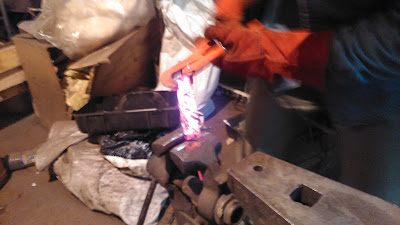
Торсируем червей в тугую косицу - чтоб им жизнь медом не казалась...
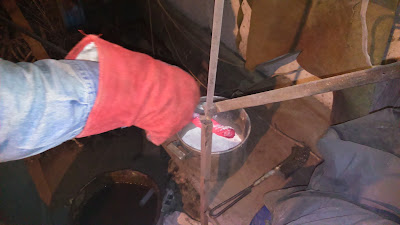
Посыпаем пакет флюсом для удаления оксида железа.
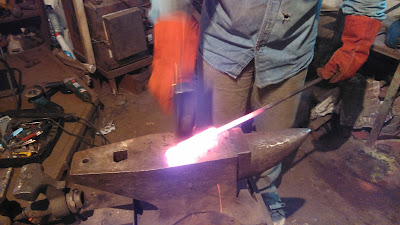
Проковываем слегонца.
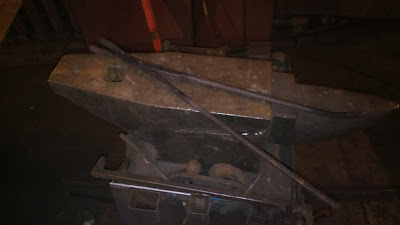
А вот, кстати, и те мои первые клещи, что я сковал по заветам Виленыча. Илья сначала раскритиковал, но потом сказал, что такая конструкция тоже имеет право на существование и даже захотел себе такие же на всякий случай - во как!
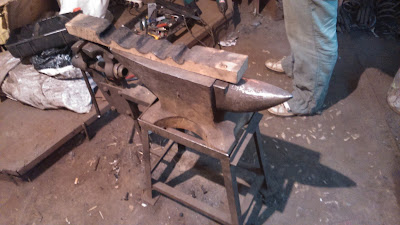
Деревянная оправка для сварки пакета. Позволяет не расползаться частям пакета, да и горение березы дольше поддерживает ковочную температуру. А мы впоследствии в Академии в таких оправках ковали (или использовали деревянные киянки) с целью пробитую на металле текстуру не нарушить. Например есть узор на одной стороне поковки, а надо другую сторону проковать и не нарушить сей узор. Вот и подкладываешь дерево - как буфер. Или деревянной киянкой бьешь по текстурированной поковке - выгнуть ее, например, если надо, или еще что... Потом все это подробнее освещу при описании дипломной работы.
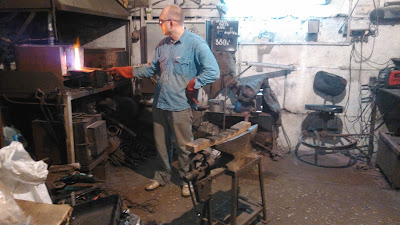
Ох сейчас начнется...
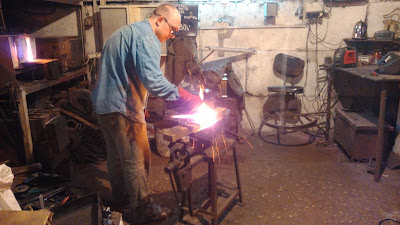
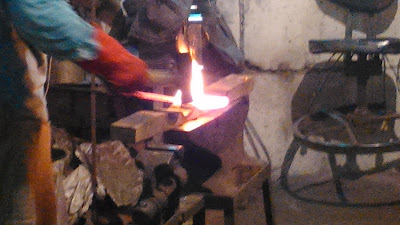
Пошла ковка в деревянной оправке! Это сущий ад! Во все стороны летит окалина - метров на 5 порой разлетается!!! Как говорил наш препод кузнец Авдеев - "ШУБИСЬ!!!"
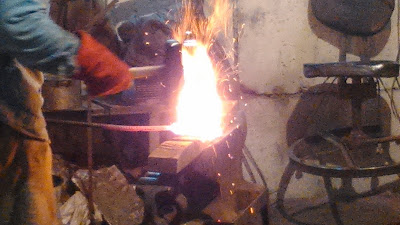
И даже вот так. Молот потом был как вороненый после сей операции...
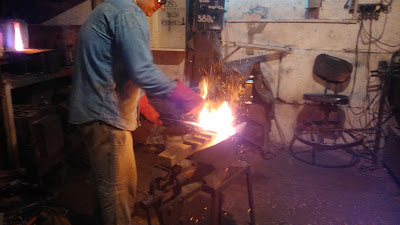
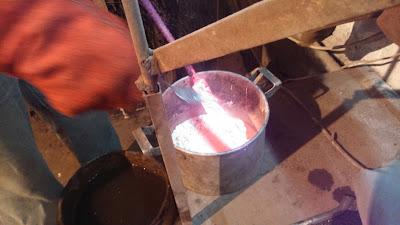
Еще немножко флюса... Операция повторяется многажды...
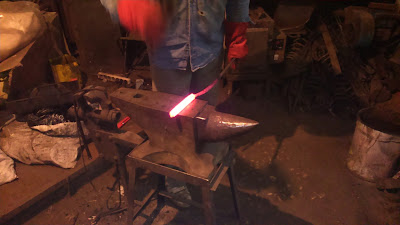
...Пока не получится вот такая чистенькая поковка.
Из нее в следующий раз будем доковывать клинок.
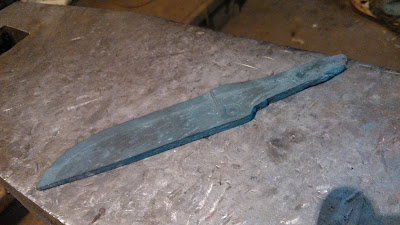
Вторая часть Марлезонского балета. Вот что получилось из того куска троса из части первой. К сожалению, процесс приварки в торец режущей кромки из У10 я пропустил. Еще напишу на сей счет подробно - как это делается, уж будьте покойны:)
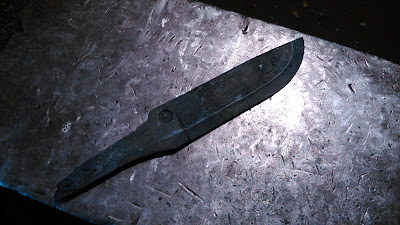
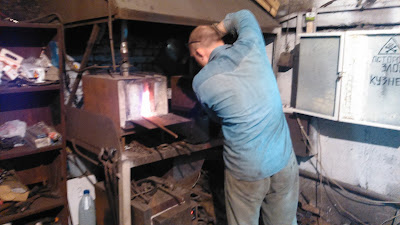
Илья закаливает тросовый клинок в масле.
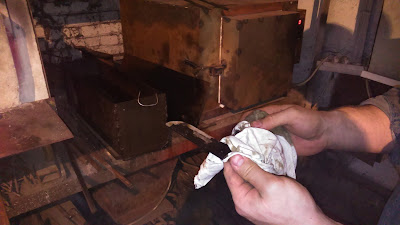
Оттирает масло.
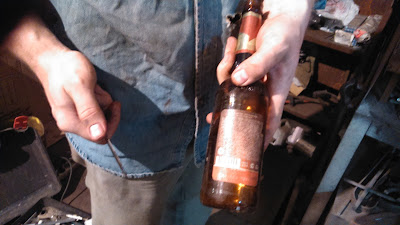
Тест на твердость - клинок легко режет бутылку.

Суем в печку для отпуска - 1 час при 200 градусах Цельсия.
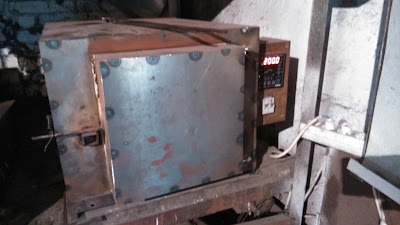
Заявленные 200 градусов. Можно и дома в духовке.
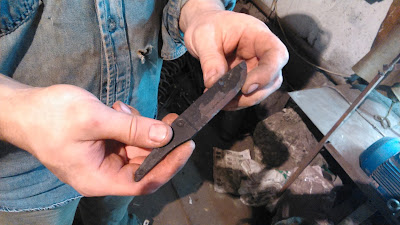
Клиночек после отпуска.
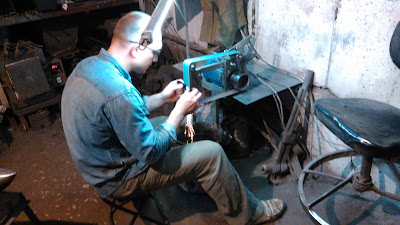
Немного слесарки на гриндере. Примерно час и 4 разные ленты:)
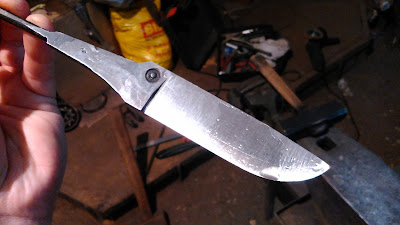
С приваренной шпилькой под резьбу на затяг. И это еще не
конечная стадия. После четвертой ленты он был идеален.
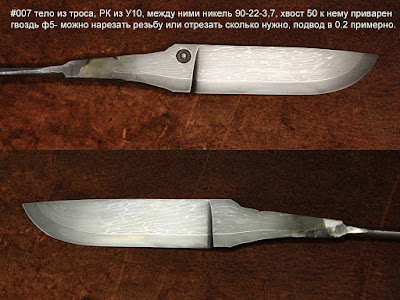
И вот этот красавец - нож из стального тросауже продается на Ганзе - улетел как горячий пирожок.
Маленьким бонус-треком к процессу ковки ножа из троса еще добавлю сюда же как мы приваривали шпильку к хвостовику клинка, что принес зашедший на огонек камрад с Ганзы. Примерно по такому же принципу приварена шпилька и на готовом ноже из стального троса вверху. Может кому пригодится. Вся фишка в особом пропиле, а не в дуговой сварке - варить то многие умеют...
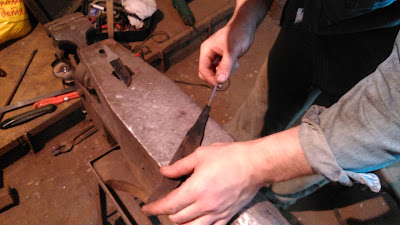
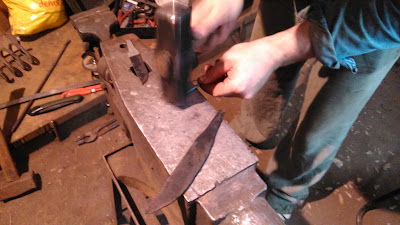
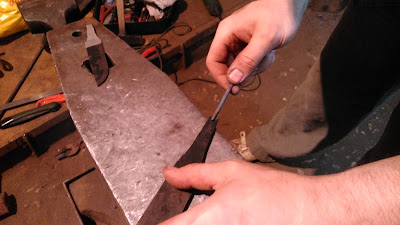
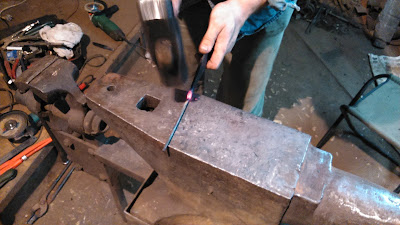
Привариваем и сбиваем окалину. Варить все умеют?
Учитесь, дело полезное:)
P.S.
Надо отметить, что те фотки, где клинок уже готов и с приваренной РК, относятся не к 3.08.2014, а к 10.08.2014. Поместил фотки с готовым клинком я сюда для того, чтобы показать результат мытарств со стальным тросом. Так то конечно Илья закаливал, отпускал и слесарил клинок уже 10.08.2014го, но в тот день я еще самолично под его контролем выковал свой первый в жизни белевский нож - от начала и до слесарки. Так что будущий отчет про свою четвертую в жизни ковку 10.08.2014го я посвящу именно белевскому ножу - полностью и целиком - дабы не делать мешанину и не сеять путаницу.www.aveursus.ru
Ковка ножа из советского вторичного сырья
Вторичное сырье не позволит сделать клинок высочайшего качества. Но многим нравится ощущение перерождения других материалов в режущие и колющие предметы. Например, ковка ножа из напильника или цепи, рессоры, клапана, подшипника, троса, сверла.
Нож из подшипника
Для ножей используются подшипники от автомобилей, обычно диаметром сантиметров 10-15.
Ножи из троса
Из троса получаются хорошие клинки, но дамасские свойства не высокие из-за крупных рисунков. Ножи из троса содержат небольшое количество углерода, поэтому к их телам нужно приваривать режущую кромку из дамаска.
Ножи из рессоры
Многие предпочитают делать ножи своими руками из рессоры, которая была изготовлена еще в советский период. Тогда использовалась для рессоры высококачественная сталь 65Г. Свойства металла рессоры повышаются за счет правильного соотношения составных частей и технологичной термообработки. Если ножи из рессоры перекалить, то они станут хрупкими.
Ножи из цепи
Широко применяется для ковки такой вторичный материал, как цепи. Чаще это цепи от бензопилы, но бывают и моторные цепи от бензинового двигателя.
Ножи из клапана
Для изготовления ножей своими руками из клапана берутся пустотелые выпускные клапаны. Не каждый умелец знает, как грамотно оттянуть нож из клапана. Поэтому это не лучший вариант.
Ножи из сверла
Хорошие ножи получаются из сверла. Инструментальная сталь, из которой изготовлены сверла, говорит сама за себя. Если правильно закалить клинок, сделанный своими руками из сверла, то он не будет ломаться при ударных нагрузках и сможет противостоять высокой нагрузке на изгиб.
Ножи из напильников
Чтобы изготовить нож из напильника своими руками нужно сначала нарисовать эскиз – форму лезвия и ручки, выбрать способ крепления, как на видео. Металлом для напильника является углеродистая сталь У10. Ее твердость составляет 57 — 58 HRC. Эти свойства металла при ковке сохраняются, и ножи из напильника получаются крепкими, с высокими режущими показателями и выдерживают большую нагрузку.
Ножи из пилы
Альтернативой может быть использование механической пилы для железнодорожного рельса. Их прочность даже выше, чем у напильников. Оба эти изделия как нельзя лучше подходят для ковки ножей в домашних условиях. Так как старый напильник более доступен, то технологию ручной ковки из него и рассмотрим более подробно. Также процесс можно посмотреть на видео.
Этапы переделки напильника в нож
Ковка в домашних условиях должна происходить при строгом соблюдении всех мер предосторожности.
Будем пользоваться:
- Напильником (желательно советским).
- Материалом для изготовления рукоятки (пластик, кость, дерево и др).
- Обувным кремом и воском.
- Газовой плитой или другим нагревательным устройством.
- Станком, тисками и болгаркой.
- Магнитом.
- Наждачной бумагой.
- Материалом для заклепок (желательно латунь).
- Клеем для кожи и металла.
Шаг 1
Сначала производим обжиг напильника в печи, как на видео. Накаливаем его на протяжении 6 часов и оставляем там до полного остывания. Это делаем для того, чтобы сталь стала такой, как перед заводской обработкой. Вместо печи можно использовать раскаленные угли костра. В домашних условиях для этого можно использовать газовую конфорку. На нее кладут будущий нож тем местом, где предполагается режущая часть. Сверху ставят металлический тепловой экран так, чтобы он не касался напильника. Заготовку посыпают солью, которая при нагревании должна расплавиться. Время процесса – 6 часов.
Шаг 2
Затем отрезают от заготовки все лишнее, чтобы она соответствовала нарисованному эскизу. Теперь нужно просверлить отверстия для клепок и закалить будущий нож. Заготовку равномерно прогревают до накаливания одного цвета. Рукоятку можно не закаливать. Если сталь закалилась, то она не будет магнититься. Это сигнал к дальнейшим действиям. На этой стадии заготовка должна царапать стекло, если все сделано правильно.
Шаг 3
Самая ответственная часть дела закончена, можно приступать к отпуску – процессу изменения свойств стали, с целью снижения хрупкости. Для этого нужно прогреть нож в духовке два часа. Затем нож шлифуется, доводится до гладкого состояния поверхности, как на видео.
Шаг 4
Следующим этапом будет травление стали хлорным железом. Результатом станет образование оксидной пленки, она защитит металл от коррозии. Если хлорного железа нет, то можно воспользоваться уксусом или лимонным соком.
Шаг 5
Завершающий шаг – рукоятка. Она садится на клей и приклепывается. Заточка предполагается ручная, как на видео, так как царапин нож не боится. Во всяком случае, лучше ручная заточка, чем неумелая на станке. Теперь лезвие нужно натереть воском. Затачивать ножи целесообразно до окончательной закалки металла.
Вместо накладной рукоятки можно использовать кожу, которую надо равномерно намотать и с помощью крема для обуви довести до состояния однородности.
Надо заметить, что ножи, сделанные в домашних условиях, очень устойчивы к механическим обработкам и после закалки, править их можно будет только на алмазной заточной машинке. На обычном точиле получиться поправить только ручную заточку.
Похожие статьиgoodsvarka.ru
Как сделать нож из дамасской стали
Дамасская сталь очень многогранный материал, позволяющий кузнецу множество возможностей реализовать задуманное.
Современные стали, используемые для изготовления дамаска, позволяют добиться любых желаемых свойств будущего клинка, но в современном контексте понимания дамасской стали, не менее важным, является получения красивого рисунка на металле, и здесь простор для реализации желаний гораздо больше. Высоты, которых добились многие известные мастера современности, достойны восхищения.
Но есть и другое направление в развитии дамасской стали — это использование вторичных материалов, на которых я хотел бы остановится подробней. Нужно заметить, что эти материалы не позволяют добиться от клинка сверх свойств, они больше являются пафосными материалами, но многим очень нравится концепция того, что их клинок является перерождением другого материала.
Явным фаворитом здесь, является дамаск из тросов, метал из которого, изготовлены тросы, позволяют получить неплохой клинковый материал, но за счёт крупного рисунка не даёт прироста режущих (дамасских) свойств
Рис 1. (дамск из троса с крупным рисунком)
Рис 2. (дамск из троса с мелким рисунком) Но также встречаются тросы, которые не позволят получить хороших режущих свойств (из-за малого количества углерода), в таком случае к телу клинка приваривается режущая кромка из клинкового металла или дамаска, либо изготавливается ламинат — где в центре клинковый материал, а обкладки из декоративного тросового дамаска.
Рис 3. (торцовая сварка: режущая кромка шх15, тело дамаск из троса).
Нужно также отметить, что хотя, если материал и не имеет хороших режущих свойств но в реализации, как в ламинате, так и в торцовом исполнении, трос за счёт своей упругости, позволяет на режущей кромке использовать очень твердый, но хрупкий метал, прочностные недостатки которого компенсирует упругий трос. Такой клинок быстрее согнется, нежили, сломается.
Так же широкое распространение получили такие вторичные материалы как цепи, чаще всего используют либо цепи от бензопил, либо моторные цепи бензиновых двигателей.
Рис 4.(дамаск из моторной цепи).
Более редко используются сетки, их свойства в основном схожи с тросами, описанные выше.
Рис 5. (ламинат: в центре шх15, обкладки дамаск из сетки, на фоне которой снят клинок)
Рис 6. (ламинат: в центре шх15, обкладки дамаск с использованием нержавеющей сетки).
Прежде чем приступить к изготовлению ножа, рекомендую изучить чертежи ножей, для ознакомления их конструкций.
Нужно заметить, что подобных материалов, пригодных для изготовления клинкового дамаска достаточно мало, в данной статье я хочу познакомить вас с процессом изготовления клинка из мотка проволоки. Суть данного эксперимента в получении нового рисунка на готовом клинке.
Рис 7. (моток проволоки).
Первым делом, пытаемся выяснить приблизительный химический состав проволоки, это необходимо для того, чтобы узнать, возможно, ли сварить её кузнечной сваркой и приблизительное количество углерода – это необходимо, чтобы узнать возьмёт ли готовый клинок закалку. Этот сложный анализ мы проводим достаточно просто — проверкой на искру.
Рис 8. (проверка на искру).
По искре видим, что метал, не легирован, что говорит нам о возможности её сварки горновым способом и то, что количество углерода 0,8-1%, что позволяет нам предположить, что метал, возьмёт достойную закалку. Также существует возможность выгорания углерода при горновой сварке, но это мы сможем проверить только после сварки.
Далее для удобства дальнейшей обработки, необходимо произвести отжиг, эту операцию мы проводим в муфельной печи
Рис 9. (отжиг).
Нагреваем до аустинитного превращения и даём остыть вмести с печью. После этого проволока становится мягкой.
Следующая операция — это формирование пакета для горновой сварки, так как проволока стала достаточно мягкой, мы можем её согнуть в удобную нам форму, после чего один её конец обматываем мягким железом и провариваем электродуговой сваркой. Полоска железа необходима для возможности использования электросварки, ведь проволока очень тонкая и она просто сгорела бы. После привариваем ручку из арматуры, для удобства удержания при горновой сварке и дальнейшей ковке.
Рис 10. (заготовка).
Теперь нагреваем нашу заготовку примерно до восемьсот градусов. Я использую газовый горн, он имеет ряд преимуществ как то постоянная восстановительная атмосфера и в нём всё хорошо видно, что происходит.
Рис11. газовый горн.
После чего обильно посыпаем бурой. Бура нужна для растворения окалины и защиты метала от кислорода – это важно для проведения качественной кузнечной (горновой) сварки. После чего проводим непосредственно саму сварку
Рис 12. (посыпание бурой).
Сварку проводим на бруске дерева, это необходимо для защиты заготовки от кислорода, огонь появившийся от контакта заготовки и дерева, выжигает кислород и создаёт восстановительную среду вне горна. А также для меньшей теплоотдачи заготовке – то есть проволока очень тонкая и при контакте с наковальней быстро остывает.
ис 13. (сварка).
После горновой сварки, расковываем заготовку до необходимых размеров, в данном случае мы собираемся заготовку торсировать (скручивать) – поэтому расковываем в квадрат со стороной двадцать мм. Измеряем воротком, – которым будет скручиваться заготовка.
Рис 14. (расковка).
Рис 15. (подготовка к торсировке).
Теперь, когда мы подготовили заготовку, важно придумать, как будет вскрываться рисунок, на данном этапе волокна расположена в вдоль заготовки и конечное изделие будет не очень эффектным. Можно его скрутить – но тогда получится такой же рисунок металла, как и у обычного троса, поэтому в данном случае скручиваем в разные стороны с шагом примерно полтора два сантиметра
Рис 16. (торсировка).
Рис 17. (торсировка).
После чего заготовку подравниваем до нужных размеров, в данном случае размер квадрата примерно двадцать миллиметров.
Рис 18. (заготовка после торсировки).
Рис 19. (заготовка после торсировки).
Когда заготовка готова, пришло время выковать клинок. Оттягиваем тело, носик будущего клинка и хвостовик. Можно также выковать спуски, но в таком случае рисунок металла вскроется слабо.
Рис 20. (клинок после ковки).
Рис 21. (клинок после ковки).
Шлифуем будущий клинок и подравниваем торцы
Рис 22 (заготовка).
После чего ставим клеймо, привариваем хвостовик и размечаем будущие спуски
Рис 23. (заготовка).
Рис 24. (заготовка).
После чего на гриндере, грубо формируем спуски.
Рис 25. (клинок перед закалкой).
Пришло время термообработки. Делаем нормализацию, для того, что бы убрать напряжения от ковки и измельчить зерно металла. Далее закалка: нагреваем в закалочном горне до температуры закалки и опускаем в ёмкость с подогретым до семидесяти градусов маслом. После чего проводим отпуск – нагрев до температуры двести градусов и выдержкой два часа.
Рис 26. (закалочный горн).
Рис 27. (закалка ножа).
Рис 28. (клинок после закалки).
Теперь шлифуем нож на чисто и протравливаем его в пяти процентном растворе хлорного железа – это необходимо, что бы проявить рисунок. В итоге получаем такой клинок
Рис 29. (готовый клинок) – который мой знакомый окрестил «Стихия».
Рекомендуемые статьи
Нашли что-то интересное? Поделись с друзьями:
rusurvive.ru
Ржавый трос добавил на 3 стр.
Добрый день.Принес знакомый ржавый трос длиной 1 метр,пролежавший в реке лет 15-20, посмотрел на него и решил сватить из него клиночки. Кузнечную сварку проводил на древесном угле. Первые сварки металл вел себя как пластилин, но при наборе слоев около 1000 метал на много стал жестче и стал упругим. В итоге получилась пару небольших клиночков. Один клинок одел:Клинок длиной 123 мм, ширина у рукояти 26 мм, толщина у рукояти 3,8 мм, к острию обух на клин, спуски прямые от обуха до 0,3мм.Рукоять выполнена из ясеня, пропитана тунговым маслом, покрыта данишем, длина рукояти 123 мм. Больстер латунь.Ножны кожа (шведка) окрашена в черный свет.
И небольшой обзор по резу каната https://www.youtube.com/watch?v=Md0f-tXTR48
Nikolaich72 16-09-2013 10:55Нож понравился,только не совсем понимаю-зачем для троса столько слоёв?В итоге оригинальный рисунок убит напрочь.Хотя думаю есть и полезный момент-если поначалу металл был как пластилин,а потом стал более упругим,вероятнее свего произошло науглероживание металла.В любом случае респект,хотя бы за проделанную работу!
lider7 16-09-2013 11:46Нож мне тоже понравился своей красотой, чистотой форм и ощущением большой надежности.Немного не понимаю...Чтобы получить 1000 слоев, необходимо достаточно большое колличество кузнечных сварок. При каждой сварке С будет немного уходить, что плохо сказывается на рабочих качествах ножа.У вас же (с удовольствием посмотрел ролик) , нож режет очень агрессивно, можно сказать люто. Или как-то "науглеродили" ?
Вова_Н 16-09-2013 11:54Хороший ножик, понравился. Если посильней протравить, то рисунок получше станет?
Nikolaich72 16-09-2013 12:01quote:Originally posted by lider7:Чтобы получить 1000 слоев, необходимо достаточно большое колличество кузнечных сварок. При каждой сварке С будет немного уходить, что плохо сказывается на рабочих качествах ножа.Чтобы получить 1000 слоёв для троса не надо делать большое количество сварок.Каждая проволочка в тросе-это уже слой.Допустим в тросе 6 прядей по 37 проволочек в каждой в итоге получимв исхлдном пакете 222 слоя и чтобы получить в готовом изделии 1000 условных слоёв надо произвести где-то 4 сварки.К тому же при ковке на древесном угле(особенно сосновом,если верить литературе) металл наулероживается.Так что ничего удивительного.alex-wolff 16-09-2013 12:04симпатично.
lider7 16-09-2013 12:05Понял, спасибо
Коля.Б 16-09-2013 12:21quote:Originally posted by :[B][/B]Сварок было сделано 6:1-трос на горячию закручен сварен, вытянут в полосу2-готовая полоса разрезалась на 4 части и проваривалась итог 4 слоя3- брусок с 4 слоями резался на 4 части и проваривался итог 16 слоев4- брусок с 16 слоями резался на 4 части и проваривался итог 64 слоя5- брусок с 64 слоями резался на 4 части и проваривался итог 256 слоев6- брусок с 256 слоями резался на 4 части и проваривался итог 1024 слоя
Коля.Б 16-09-2013 12:25quote:Originally posted by Вова_Н:Если посильней протравить, то рисунок получше станет?Не станет, обычно 2-3 минут хватает для травления в хлорном а этот клин где то минут 7 травил. Да и клин закален полностью всем телом
Nikolaich72 16-09-2013 12:28quote:Originally posted by Коля.Б:Не станетСогласен полностью.Если рисунок есть то его видно сразу.Увеличивая время травления получим глубокий рельеф,а это не совсем хорошо.Nikolaich72 16-09-2013 12:31quote:Originally posted by Коля.Б:1-трос на горячию закручен сварен, вытянут в полосу2-готовая полоса разрезалась на 4 части и проваривалась итог 4 слоя4 условных слоя.Весь вопрос в том,сколько проволок было в изначальном тросе?M cCar 16-09-2013 13:03Ножик приятныйРисунок не впечатлил. А по резу то ,по резу то что получилосьКак этот трос режет и твердость какая ?
После фотографий в теме прикреплена ссылка на видео, вот и по ней посмотреть можно как режет
Xlopchik 16-09-2013 16:58формы ножа очень приятные, красавец
TodderWolfe 16-09-2013 17:40Понравился!
Древесный уголь 16-09-2013 18:37Очень понравился! Замечательный, гармоничный нож. Отдельная похвала по дамаску - 1000 слоёв - великий труд, но так и должно быть!
AprioriTerra 26-09-2013 20:18Понравился, видео смотрел.
GMX[23RUS] 11-10-2013 13:26Всегда в таких темах интересует вопрос: при сварке чем ковали? Вручную али механизация какая была?
GMX[23RUS] 11-10-2013 13:26Всегда в таких темах интересует вопрос: при сварке чем ковали? Вручную али механизация какая была?
Антон42 11-10-2013 14:45Отличный нож!А на этом же канате другие стали тестировали?
Антон42 11-10-2013 14:52Так же порадовала правка после каната, вжик вжик и по новой Не, ну Молодец, что тут скажешь!!!!
Респект!
Скажите, ясень обычный или какой-то особенный? Просто у нас на рынке виделчеренки для топоров из ясеня, но рисунок там совсем другой.
AlexDelf 11-10-2013 20:11Замечательно! Ножны б темно-коричневые сюда))Сколько стоит?
Шалим 11-10-2013 20:35Достойно.Уважаю, когда из говна (старый ржавый трос), делают канфету - нож.Нож понравился.
Old Tramp 12-10-2013 10:05Хороший рабочий нож. Понравился.
Коля.Б 12-10-2013 11:00quote:Originally posted by GMX[23RUS]:Всегда в таких темах интересует вопрос: при сварке чем ковали? Вручную али механизация какая была?При сварке мех. молот, а формировка с оттяжкой спусков в ручную.
Коля.Б 12-10-2013 11:01quote:Originally posted by Антон42:Отличный нож!А на этом же канате другие стали тестировали?CPM S35VN не больше резов сделал. Видео снимал время как появится сожму и выложу.
Коля.Б 12-10-2013 11:05quote:Originally posted by Антон42:Так же порадовала правка после каната, вжик вжик и по новой

По ножнам так и хотел, красил сразу двое ноже одни черные вторые хотел коричневые, но по запарке все окрасил в коричневый.по стоимости тема в барахолке http://guns.allzip.org/topic/94/1238142.html нож уехал в г. Колпашево, Томской области.
Коля.Б 12-10-2013 11:11quote:Originally posted by Dimon8800:Скажите, ясень обычный или какой-то особенный? Просто у нас на рынке виделчеренки для топоров из ясеня, но рисунок там совсем другой.если быть точным то это ясень оливковый.
Dimon8800 12-10-2013 16:58quote:Originally posted by Коля.Б:если быть точным то это ясень оливковый.а не подскажете где такой можно достать в городе, в каких магазинах такоеможет продаваться?Павел Быков 74 12-10-2013 18:03Такую работу за такую цену ???? Сам работаю на древеснике и знаю,что это такое.Но ценить себя нужно.С уважением П.Быков.
Коля.Б 12-10-2013 19:15quote:Originally posted by Dimon8800:а не подскажете где такой можно достать в городе, в каких магазинах такоеможет продаваться?в этой теме брал http://guns.allzip.org/topic/189/706869.html
Коля.Б 12-10-2013 19:19quote:Originally posted by Павел Быков 74:Такую работу за такую цену ???? Сам работаю на древеснике и знаю,что это такое.Но ценить себя нужно.С уважением П.Быков.При первой цене ни каких предложений не было, а купил его постоянный клиент, который знает толк в рабочих ножах... И так в Томске часто слышу что дорого!!!
Алешенька1986 12-10-2013 19:36Нож из троса?то есть получается из любой хмм..железки можно получить клинок? только не факт что он будет хорошим я верно понял ?просто давно такой вопрос зрел
Бысь 12-10-2013 21:07quote:то есть получается из любой хмм..железки можно получить клинок? только не факт что он будет хорошим я верно понял ?Я не большой специалист в этом деле, но насколько я знаю тросы делают из стали, обладающей большой гибкостью и неплохой коррозионной стойкостью. Так что клинок по факту должен быть неплохой). Наверняка тут есть те ,кто сможет обьяснить подробнее.Павел Быков 74 13-10-2013 14:23quote:При первой цене ни каких предложений не было, а купил его постоянный клиент, который знает толк в рабочих ножах... И так в Томске часто слышу что дорого!!!А ты предложи им покупать в Нижнем Новгороде-много и дёшево !!!Nasgul 13-10-2013 14:43Лаконичная красота-респект!
Коля.Б 13-10-2013 15:35quote:Originally posted by Павел Быков 74:А ты предложи им покупать в Нижнем Новгороде-много и дёшево !!!Это точно, но я их обычно в тайгу отправляю...vityuxa 13-10-2013 16:56Качественная, отлично проделанная работа, и итог прекрасен! Нож в своей простоте - просто красавец! А то, что из г... конфетку замостырили ещё + 100 респектов!
Коля.Б 13-10-2013 17:30quote:Originally posted by vityuxa:Качественная, отлично проделанная работа, и итог прекрасен! Нож в своей простоте - просто красавец! А то, что из г... конфетку замостырили ещё + 100 респектов!Спасибо.
Коля.Б 13-10-2013 17:35quote:Originally posted by Алешенька1986:Нож из троса?то есть получается из любой хмм..железки можно получить клинок? только не факт что он будет хорошим я верно понял ?просто давно такой вопрос зрелНа счет хмм.. не чего не скажу, хотел сделать инистое железо, прикинул что наиболее проржавевшее железо только трос, который пролежал на берегу реки не один десяток лет. Павел Быков 74 13-10-2013 17:55quote: хотел сделать инистое железоИ получилось !!!Большой Бро 13-10-2013 18:25Про заточку тоже интересно. Были такие моменты, когда нож доведеный до бритья - выдыхался сразу же, после грубого камня резал как сумашедший. ИМХО если нож держит РК при заточке самым мелким камнем - сталь хорошая, соответственно он будет резать и при другой заточке. На углеродках это работает.
Алешенька1986 13-10-2013 19:36Отличнейшая работа вами проделана!!!И мое мнение у вас действительно получилось задуманное!
ДокВВ 13-10-2013 21:05прекрасные линии обриса. просто и с большим вкусом.
Коля.Б 24-11-2013 20:36Клинок из даммаской стали (исходный материал ржавый трос) количество слоев около 1000, пакет варился на древесном угле, длина клинка 129 мм, ширина у рукояти 26 мм, толщина 3,9 мм., к острию сужается. Спуски прямые от обуха сведены до 0.2 мм.Рукоять выполнена из ореха, капа березы, вставки из коры бивня мамонта, больстер и проставки из мельхиора. Рукоять пропитана тунговым масло и покрыта данишем, монтаж сквозной, рукоять стянута мебельной стяжкой, проклеена суперхватом. Длина рукояти 122 мм.Ножны кожа растительного дубления толщиной 3 мм, пропитаны льняным маслом.
Небольшое видео по резу канатаhttps://www.youtube.com/watch?v=2JPZoO1sd7o
Лемминг 24-11-2013 21:42Классная реинкарнация троса получилась!!!
метадум 24-11-2013 23:13Такое из старого троса! Восхитительно!
Да ещё и наиспытывать столько.
guns.allzip.org