Стекломат – волокнистые наполнители для ПКМ. Стекломат что такое
Группа компаний композит - Стекломаты от Группы компаний "Композит"
Рулонный стекломат представляет собой материал, изготовленный из рубленого ровинга – плотного стекловолоконного жгута. Волокна ровинга связаны между собой благодаря специальной клеевой основе. Типы стекломата различают по основе для склейки отрезков ровинга, а также по поверхностной плотности готового полотна. Сегодня в промышленности активно используются порошковый и эмульсионный стекломаты. Предназначен стекломат для изготовления стеклопластиков на основе полиэфирных смол. Функция - армирующий материал.
Эмульсионный стекломат изготавливается из рубленых нитей стекловолокна Е-типа, содержащего низкий процент щелочи. Поверхностная плотность стекломата 225, 300, 450, 600, 900 г/м2.Данный стекломат применяются при ручном формовании стеклопластика, при производстве стеклопластика по технологии закрытого формования. Изделие характеризуется высоким качеством и легким высвобождением воздуха в процессе ламинирования. Ламинаты, изготовленные из данных стекломатов, в течение длительного периода демонстрируют хорошие механические свойства и высокую устойчивость к атмосферным воздействиям.
Свойства:
-
Легкое удаление воздуха из материала;
-
Хорошая поверхностная сшивка и высокая полнота нитей;
-
Отличная драпируемость;
-
Быстрое смачивание и пропитываемость;
-
Легкий в обращении;
-
Малое потребление смолы;
-
Хорошо совмещается с ненасыщенными полиэфирными смолами.
Порошковые стекломаты изготавливаются из нарезанной нити стекловолокна, склеенной порошкообразным наполнителем. Этот стекломат изготовлен из стекла Е-типа с содержанием щелочей меньше 1 %. Поверхностная плотность стекломата 225, 300, 450, 600 г/м2.Порошковые стекломатериалы характеризуются быстрой пропитываемостью ненасыщенными полиэфирными смолами, стабильностью качества и удобством применения. Ламинаты, изготовленные из данного стекломатериала, прозрачные, гладкие, обладают повышенной механической и атмосферной стойкостью.Стекломаты используется для горячего ламинирования как механическим, так и контактным способом. Используется для производства крупных несложных изделий из ненасыщенных полиэфирных смол, наполненных стекловолокном, при изготовлении сухих заготовок (преформ) для изготовления стеклопластика по технологии закрытого формования. Изделия можно получать очень гладкие и прозрачные. Вышеуказанные стекломатериалы применяются, прежде всего, в строительстве дорог, судостроении.
Длинноволокнистый мат состоит из нескольких слоев случайным образом направленных прядей, связанных друг с другом подходящим связующим. Данный мат сочетает в себе электрические и механические свойства традиционного Е-стекла с коррозионной стойкостью E-CR стекла. Используется в технологии пултрузии, процессах закрытого формования, изготовления преформ. Поверхностная плотность такого мата составляет 100-900 г/м2.
Если не указано иное, стекломат рекомендуется хранить в прохладном и сухом месте. Температура не должна превышать 350 С, а относительная влажность должна поддерживаться ниже 75%. Стекломат должен оставаться в своем упаковочном материале непосредственно до момента использования. Необходимо избегать повреждения упаковочного материала стекломата при хранении. При попадании влаги в стекломат он становится непригодным для дальнейшего использования.
За более подробной информацией по видам стекломатериалов обращайтесь в любое представительство группы компаний "Композит".
composite.ru
Полезная информация для изготовления стеклопластика
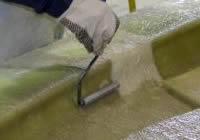
Стеклопластик это материал, состоящий из двух основных компонентов. Это материал из стекловолокна (стекловолокно, стеклоткань, стекломат), который служит для армирования (усиления) изделия, и смолы, являющейся связующим.
Материалы для изготовления стеклопластика.
Смола
Смола является связующим материалом и поэтому к выбору смолы надо подойти наиболее ответственно, особенно при отсутствии опыта изготовления стеклопластиковых изделий. Если при выборе стеклоткани или стекломата можно довольствоваться рекомендациями специалистов, т.к. этим выбором определяются, в основном, механические свойства готового изделия, то разная смола требует разных технологических процессов.
Для начинающих мы рекомендуем эпоксидную смолу. Эпоксидная смола менее привередлива в работе и имеет большее время застывания и поэтому у вас будет больше времени для исправления возможных ошибок. Эпоксидную смолу также рекомендуется использовать при ремонте изделий (лодок, бамперов…). Она хорошо склеивается с пластиком, деревом, металлом.
Полиэфирная смола, в основном, используется для изготовления цельных деталей
Хотим также напомнить, что на свойства смол и на их рабочие параметры довольно сильно влияют температурные характеристики помещения, в котором производятся работы, и его проветриваемость. Порой для лучшего застывания матрицу с изделием помещают в специальную сушильную камеру. Это помогает значительно ускорить процесс получения готового изделия. Самые прочные изделия изготавливаются в автоклавах под большим давлением и при высокой температуре.
Сама смола достаточно хрупкая, и именно стекломатериал придает ей необходимую прочность и гибкость
Материалы из стекловолокна
Для изготовления стеклопластиков используется стекловолокно, ровинг, стекломат, стеклоткань и другие стекломатериалы.
Самые распространенные это ровинг, стекломат и стеклоткань.
Ровинг
Ровинг это стекловолокно собранное в пучок и намотанное на бобину. Ровинг похож на некрученую стеклонить. Укладка ровинга производится специальным пистолетом, в который, во время работы, подается еще смола и катализатор.
Стекломат
Стекломат состоит из хаотично расположенных волокон, а стеклоткань выглядит как обычная ткань. Наибольшее упрочнение дают стеклоткани. Стекломаты дают меньшую прочность, но они более легки в обработке и по сравнению со стеклотканью лучше повторяют форму матрицы.
Стекломат может быть очень тонким, а бывает толстым, как одеяло. Стекломаты различаются по толщине и плотности, но разделяют их по весу одного квадратного метра материала в граммах: 300, 450, 600. Чем тоньше мат, тем более сложную поверхность он позволяет вывести, с большим количеством граней и резких переходов. Толстый мат (600 или 900) позволяет набрать толщину изделия и добиться необходимой прочности. При создании толстых изделий работа проходит в несколько этапов. Выкладывается несколько листов для получения первого слоя и дается время на застывание. Затем дополнительно, уже на твердую поверхность, укладываются дополнительные листы мата для придания необходимой толщины. Если попытаться уложить сразу все слои, то велика вероятность, что готовое изделие покоробится, стянется.
Стеклоткань
Стеклоткани бывают разной толщины. Стеклоткани также используются для придания жесткости и объема готовому изделию. Как и любая ткань, стеклоткань неодинаково работает при разнонаправленном растяжении. Поэтому для придания необходимой жесткости стеклоткань укладывается под разными углами. Стекловолокно в стеклоткани играет немаловажную роль. Оно должно хорошо пропитываться смолой и удерживать ее между волокнами. На это свойство пропитываемости в стеклоткани влияет наличие в ней и количество парафина. На ответственные изделия желательно выбирать стеклоткани без парафина. Парафин также можно выжигать перед применением.
К слову о прочности. Как это ни странно прозвучит, но чем меньше смолы в стекловолокне (при условии его полной пропитки и отсутствии пузырьков), тем прочнее будет готовое изделие и тем меньше окажется и его вес.
Гелькоут (gelcoat)
Для придания цвета готовой детали , а также для защиты от внешних воздействий используется особый материал гелькоут (gelcoat – гелевое покрытие). Можно сказать, что гелькоут это та-же смола, но с добавлением красителя. Его можно подобрать по цвету или создать свой оттенок колеровочными составами. Кроме того, слой гелькоута увеличивает срок службы изделия, защищает от воздействий окружающей среды и скрывает структуру стеклопластика. Готовое изделие будет иметь ровную (зависит от качества матрицы) поверхность, нужного цвета.
Гелькоуты бывают внутренними и внешними (topcoat).
Внутренний гелькоут наносится первым слоем в матрицу. После того как гелькоут затвердел, укладывается стекловолокно и смола. В этом процессе кроется один важный момент. Если слой гелькута будет в одном месте слишком тонкий, то может случиться следующее: или в этом месте будет просвечивать структура стекловолокна, или гелькоут может вообще отойти и сморщиться. Поэтому крайне важно пользоваться правильными материалами и следовать технологии. Для равномерного нанесения гелькоута часто используют не кисти, а краскопульты. Так удается значительно сократить количество брака и уменьшить расход материала. Но для распыления гелькоут должен быть более жидким, чем для ручного нанесения. В настоящее время в продаже имеются готовые гелькоуты для нанесения кистью и для напыления.
Внешний гелькоут (topcoat) наносится после того, как изделие вынули из матрицы. Здесь он выполняет роль краски. Благодаря присутствию в составе топкоута парафина поверхность после отверждения не остается липкой, хорошо шкурится и полируется. Топкоут можно изготовить самим на базе гелькоута или смолы, добавив раствор парафина в стироле.
Макет и матрица
Для изготовления изделия из стеклопластика первое, что необходимо, – создать его макет. В некоторых случаях макетом может являться уже существующее изделие, которое Вы хотите размножить. Например: бампер автомобиля. Для еще не существующих изделий макет может быть изготовлен разли
europolis.ru
Стекломат
Категория -->> Стекловолокно
Стекломат – волокнистый наполнитель для ПКМ и пластмасс конструкционного назначения. Представляет собой нетканое полотно из равномерно распределённого рубленого стекловолокна, связанного клеевой основой. Выпускается в рулонах, хорошо пропитывается эпоксидными и полиэфирными смолами, растягивается и принимает требуемые формы. В зависимости от клеящей основы и плотности полотна стекломат классифицируют на типы. Наибольшее практическое применение получили эмульсионный, порошковый и длинноволокнистый стекломат.
Стекломат эмульсионный
Сырьём для производства эмульсионного стекломата служат рубленные стекловолокна типа Е длинной до 5 сантиметров с низким содержанием щёлочи, скреплённые между собой эмульсионным связующим составом. Плотность поверхности эмульсионного стекломата составляет от 225 до 900 г/м2. Он нашёл широкое применение при ручном и закрытом методе формования стеклопластиковых изделий. Полимерно-композиционные материалы, изготовленные из эмульсионного стекломата, отличаются прочностью, устойчивы к механическим нагрузкам и не подвержены вредному химическому и атмосферному воздействию.
Преимущества эмульсионного стекломата:
- - быстрое удаление воздуха из материалов в процессе формования;
- - качественное сцепление и высокая степень наполнение стеклопластиков;
- - способность легко драпироваться;
- - хорошая совместимость с полиэфирными смолами;
- - быстрое смачивание и пропитываемость;
- - удобство применения;
- - значительная экономия полиэфирных смол.
Эмульсионный стекломат используют при производстве стеклопластиковых изделий сложной конструкций для различных отраслей промышленности: судостроение, строительство, автомобилестроение.
Стекломат порошковый
Производится из стекловолокон типа E с низким содержанием щёлочи, которые нарезают и соединяют между собой порошкообразным замасливателем. В отличие от эмульсионного, порошковый стекломат характеризуется рыхлой структурой, меньшей плотностью (100-600 г/м2) и недостаточной гибкостью.
По причине более жёсткой структуры при работе с порошковым стекломатом несколько затрудняются процессы его пропитывания и прикатывания. Применяют порошковый стекломат при производстве стеклопластиков методом прессования, вакуумной инфузии и по технологии RMT.
Порошковый стекломат нашёл широкое применение при изготовлении гладких, прозрачных, крупногабаритных стеклопластиковых конструкций, которые не отличаются сложностью форм.
Длинноволокнистый стекломат
Состоит из разнонаправленных прядей стекловолокон типа E или E-CR, которые расположены послойно и соединены между собой связующим составом. Его плотность составляет от 100 до 900 г/м2. Стеклопластик, произведённый из длинноволокнистого стекломата, характеризуется механической прочностью, коррозионной устойчивостью и улучшенными диэлектрическими свойствами. Используется преимущественно при пултрузии и закрытом методе формования стеклопластиковых пресс-форм.
Правила хранения стекломатов
Хранят стекломат в запакованном виде в сухих, прохладных помещениях, где температура не превышает 35"С, а относительная влажность воздуха - 75%. Извлекают его из упаковки непосредственно перед использованием и не допускают попадания жидкости, что может сделать его непригодным.
polycomposite.ru
Стекломат
Основные свойства стекломатов:
- Из полотна легко удаляется воздух;
- Высокий показатель поверхностной сшивки и полноты волокон;
- Хорошо драпируется;
- Легко драпируется и формуется;
- Небольшое потребление смолы.
Основное назначение стекломатов – это использование в качестве армирующего средства. Стекломат идет на производтство стеклопластиков.
Виды стекломатов:
- стекломат рубленый – это материал из рубленого ровинга (плотный стекловолоконный жгут), подготовленные части ровинга соединяются между собой клеевой смесью.
- стекломат эмульсионный – это материал из рубленых волокон стекла типа «Е» с содержанием малого процента щелочи. Ламинаты из данного вида стекломата сохраняют свои свойства в течение всего срока эксплуатации.
- стекломат порошковый – это материал из нарезанных стекловолокон из стекла типа «Е», соединенных между собой порошковым наполнителем.
- длинноволокнистый мат – это материал из хаотично направленных прядей скрепленных между собой необходимым связующим. Материал характеризуется наличием свойств стекла типа «Е» со стойкостью к коррозии стела типа «Е-СR».
Достоинства стекломатов:
- Отличное сцепление с различными видами смол;
- Хорошо смачивается;
- Легко формуется;
- Хорошее качество ламината;
- Имеет широкое распространение.
Из стекломатов изготавливают катера, лодки, яхты, корпуса, сидения, вагоны, бассейны, раковины, столешницы, материал применяется в тюнинге автомобилей и при строительстве дорог.
www.ultratkan.ru
SammaS - Стекломат
Существуют три основных типа матов из стекловолокон: маты из резаных нитей, из непрерывных нитей и декоративные маты или покрытия.
Стекломат - представляет собой нетканое полотно, получаемое резкой стекловолокон или непрерывного жгута на штапельки длиной 25-50мм. Волокна имеют преимущественно случайное распределение в горизонтальной плоскости и связанных друг с другом полимерным связующим (порошковым либо эмульсионным). Плотность таких матов составляет 0,229...0,916 кг/м2.
Маты, получаемые из нерезаных непрерывных жгутов стекловолокна раскладываются и соединяются в виде спирали. Такие маты достаточно упруги при сравнительной разреженности структуры, а благодаря механическому переплетению не требуют дополнительной связи для создания необходимой прочности.
Декоративные маты (стекловуаль) - это очень тонкие маты из простых, непрерывных мононитей. Они используются как декоративные поверхностно-армированные слои при получении композитов методом ручной выкладки или при расплавном прессовании как компонент отделки и армирования поверхности.
Стекломаты используют для производства стеклопластикового ламината. Такой ламинат практичен, так как в течении довольно длительного срока эксплуатации демонстрирует хорошие механические качества. Для различных целей применяют различные виды стекломатов, но самым популярными остаются стекломаты из стекла типа "E" плотностью 300, 450, 600 г/м2.Стекломат возможно применять с любыми видами смол: эпоксидной, полиэфирной, винилэфирной, замасливатель отлично растворим в стироле.Основные преимущества стекломата:- хорошая адгезия с различными видами смол- быстрая смачиваемость- легкость применения (в том числе и для ручного формования)- высокое качества готового ламината- широкий спектр применения
Виды изделий из стекломатов:- яхты, лодки, катера- вагоны, корпуса, антивандальные сиденья- столешницы, раковины из искусственного камня, бассейны, ванны, ограждения, перила и т.д.- различные элементы тюнинга автомобилей (бампера, спойлеры, обтекатели и др.)
sammas.ru
Большая Энциклопедия Нефти и Газа, статья, страница 1
Стекломат
Cтраница 1
Стекломаты из непрерывных волокон получают выкладкой непрерывных крученых прядей, соединяемых связующим. Стекломаты на основе рубленого стекловолокна с произвольным взаимным расположением армирующих волокон содержат волокна длиной 38 - 50 8 мм, соединенные связующим. [1]
Стекломаты изготавливаются из рубленой ровницы или из штапельного волокна, получаемого дутьевым методом. [3]
Стекломаты используются для производства сложных крупногабаритных изделий. Однако вследствие недостаточной прочности стекломатов не рекомендуется прессовать из них глу - - бокие изделия двоякой кривизны. В этом случае более целесообразно применять рубленое ( волокно. [4]
Стекломат толщиной 0 25 мм, используемый для армирования поверхностного защитного слоя, должен быть изготовлен из химически стойкого стеклянного волокна марки С или из стеклянного волокна аналогичного состава. [5]
Стекломаты применяют для теплоизоляции строительных конструкций, оборудования и трубопроводов температурой поверхности от - 60 до 150 С. [6]
Стекломаты при монтаже на корпус судна накалывают на приваренные к корпусу металлические шпильки из 3-мм проволоки. Поверх матов укладывают гидроизоляционную бумагу, которую в местах прохода через нее шпилек или других деталей прорезают по месту, а затем заделывают той же бумагой. [7]
Стекломаты представляют собой слой стеклянных волокон толщиной не более 22 мк, обшитых стеклотканью и простеганных стеклонитями. Толщина стекломатов в кузове машинного отделения составляет 30 мм. В стенке, изолирующей кабину от дизельного помещения, и полах кабины применены стекломаты толщиной 80 - 85 мм. [9]
Стекломаты ( АСИМ, АТИМС, АТМ-3) - материалы, состоящие из стекловолокон, расположенных между двумя слоями стеклоткани или стек-лосетки, простеганной стеклонитками. [10]
Пропитанный стекломат обкладывают с двух сторон полиэтиленовой пленкой и уплотняют между валками. [12]
Стекломат данной марки - слой штапельного стеклянного волокна, связанный заполимеризованным бакелитовым лаком ИФ. [13]
Стекломатами называются стекловолокнистые материалы из коротких рубленых или штапельных волокон, расположенных в полимерном связующем неориентированно, беспорядочно. Такие стеклопластики с неориентированной волокнистой структурой обладают низкой механической прочностью ( прочность стекломатов на полиэфирных смолах обычно не превышает 10 - 15 кгс / мм. Стекломаты практически изотропны по своим механическим свойствам в плоскости листа. [15]
Страницы: 1 2 3 4
www.ngpedia.ru
SammaS - Типы стеклянных волокон
Все стеклянные волокна условно можно разделить на два больших класса: дешевые волокна общего применения и дорогостоящие волокна специального применения. Почти 90 % всех стеклянных волокон, которые выпускаются сегодня в мире это стекловолокно марки Е. Подробно требования к таким волокнам изложены, например, в стандарте ASTM D578-98. Остальные 10% процентов – это волокна специального назначения. Большинство марок стекловолокна получили свое название благодаря своим специфическим свойствам:
‐ Е (electrical) – низкой электрической проводимости; ‐ S (strength) – высокой прочности; ‐ AR (alkali resistant) – высокая щелочестойкость; ‐ D (dielectric) – низкая диэлектрическая проницаемость; - Кварцевое стекло - значительная термическая стойкость; ‐ C (chemical) – высокой химической стойкости; ‐ M (modulus) – высокой упругости; ‐ А (alkali) –высокое содержание щелочных металлов, известково-натриевое стекло.
Для электрической изоляции применяется только бесщелочное (или малощелочное) алюмосиликатное или алюмоборосиликатное стекловолокно. Для конструкционных стеклопластиков, как правило, используют бесщелочное магнийалюмосиликатное или алюмоборосиликатное стекловолокно. Для стеклопластиков неответственного назначения можно употреблять и щелочесодержащее стекловолокно.
Механические характеристики стекловолокон напрямую зависят от метода производства, химического состава стекла, температуры и окружающей среды. Самую большую прочность имеют непрерывные стекловолокна из бесщелочного и кварцевого магнийалюмосиликатного стекла. Повышенное содержание щелочей в исходном стекле значительно снижает прочность стекловолокон.
Тип волокна | Состав, масс. % | ||||||||||||
SiO2 | B2O3 | Al2O3 | CaO | MgO | ZnO | TiO2 | ZrO2 | Na2O | K2O | Li2O | Fe2O3 | F2 | |
E (с бором) | 52-56 | 4-6 | 12-15 | 21-23 | 0,4-4 | - | - | 0,2-0,5 | 0-1 | 0-0,2 | - | 0,2-0,5 | 0,2-0,7 |
E | 59-60 | - | 12-13 | 22-23 | 3-4 | - | - | 0,5-1,5 | 0,6-0,9 | 0-0,2 | - | 0,2 | 0,1 |
S | 60-65,5 | - | 23-35 | 0-9 | 6-11 | - | - | 0-1 | 0-0,1 | - | - | 0-0,1 | - |
AR | 58,3-60,6 | - | 0,2 | - | - | - | 0-2,8 | 18,1-21,2 | 13,0-14,1 | 0-2,8 | - | - | - |
ECR | 58,2 | - | 11,6 | 21,7 | 2 | 2,9 | 2,5 | - | 1 | 0,2 | - | 0,1 | - |
D | 72-75 | 21-24 | 0-1 | 0-1 | 0,5-0,6 | - | - | - | 0-4 | 0-4 | - | 0,3 | - |
Кварц | 99,5-99,9 | - | - | - | -- | - | - | - | - | - | - | - | - |
Базальт | 47,5-55,0 | - | 14,0-20,0 | 7,0-11,0 | 3,0-8,5 | - | 0,3-2 | - | 2,5-7,5 | 2,5-7,5 | - | 7,0-13,5 | - |
Таблица 1. Химический состав некоторых стекол для получения непрерывного волокна.
Свойство | Тип волокна | |||||||
Е (с бором) | Е (без бора) | S | AR | ECR | D | Кварц | Базальт | |
Температура формования, °С | 1160-1196 | 1260 | 1565 | 1260-1300 | 1213-1235 | - | 2300 | 1350-1450 |
Температура размягчения, °С | 830-860 | 916 | 1056 | - | 880 | 770 |
| 1100-1200 |
Температура плавления, °С | 1066-1077 | 1200 | 1500 | 1180-1200 | 1159-1166 | - | 1670 | 1200-1300 |
Плотность, г/см3 | 2,54-2,55 | 2,62 | 2,48,2,49 | 2,6-2,7 | 2,66-2,68 | 2,16 | 2,15 | 2,67 |
Коэффициент линейногорасширения, 10-6 С-1 | 4,9-6 | 6 | 2,9 | 7,5 | 5,9 | 3,1 | 0,54 | - |
Диэлектрическая постоянная (20 С, 1 МГц), Ф/м | 5,86-6,6 | 7 | 4,53-4,6 | - | 3,56-3,62 | - | 3,78 | - |
Прочность, МПа | 3100-3500 | 3100-3500 | 4380-4590 | 3100-3500 | 3100-3500 | 2410 | 3400 | 2700-3500 |
Модуль упругости, ГПа | 76-78 | 80-81 | 88-91 | 72-74 | 80-81 | 52 | 69 | 70-90 |
Удлинение до разрыва, % | 4,5-4,9 | 4,6 | 4,5-4,9 | 2-2,4 | 4,5-4,9 | - | 5 | 3 |
Таблица 2. Физико-механические свойства некоторых марок стеклянного волокна.
Стекло E
Химический составНа сегодняшний день в мире выпускается 2 типа стекловолокна марки E. В большинстве случаев E-стекло содержит 5-6 масс. % оксида бора. Современные экологические нормы в США и Европе запрещают выброс бора в атмосферу. В то же время известно, что в процессе стеклообразования, а также в последующих процессах стекловарения происходит обеднение стекломассы некоторыми компонентами за счет их улетучивания. Из компонентов шихты наибольшей летучестью обладают борная кислота и ее соли, оксид свинца, оксид сурьмы, селен и некоторые его соединения, а также хлориды. Летучесть, рассчитанная на 1% содержания оксида в обычных стеклах, составляет для отдельных оксидов в масс. %: Na2O (из Na2CO3) – 0.03, К2О (из K2CO3) – 0.12, В2О3 – 0.15, ZnO – 0.04, РbО – 0.14, CaF2 – до 0.5. Таким образом, современные предприятия вынуждены устанавливать у себя дорогие системы фильтрации.
В качестве альтернативы возможно получение Е-стекол, не содержащих бора на основе системы SiO2–Al2O3–CaO–MgO.
Коммерческое стекловолокно марки Е получают на основе системы SiO2–Al2O3–CaO–MgO–B2O3 или системы SiO2–Al2O3–CaO–B2O3. Продукты, полученные на основе последней системы, как правило, все-таки содержат небольшое количество оксида магния (до 0,6 масс. %), что связано с особенностями сырья, которое использую для получения стекол.
Важно отметить, что точный состав стекловолокна Е может отличаться друг от друга не только для разных производителей, но даже и для разных заводов одной компании. Это обусловлено прежде всего географическим расположением предприятия и, как следствие, доступностью сырья. Кроме того на разных предприятиях осуществляется разный контроль за технологическим процессом и методы его оптимизации.
Состав борсодержащего стекловолокна и стекловолокна без оксида бора значительно отличается друг от друга. Содержание оксида кремния в борсодержащих стеклах марки Е составляет 52-56 %. Для стекловолокна без оксида бора содержание оксида кремния несколько выше и лежит в интервале 59-61 %. Содержание оксида алюминия для обоих типов стекла Е близко и составляет 12-15 %. Содержание оксида кальция также отличается незначительно – 21-23 %. Содержание оксида магния в стекле варьируется в широких пределах. Для стекол, полученных на основе тройных систем, оно составляет менее 1%, и является следствием неоднородности сырья. В случае если в состав шихты входит доломит содержание оксида магния может достигать 3,5 %.Отличительной особенностью Е-стекол, не содержащих бор, является повышенное содержание в них оксида титана – от 0,5 до 1,5 %, в то время как в классическом Е стекле его содержание находится в пределах 0,4-0,6 %.
Особенности полученияТемпература получения волокон из борсодержащего Е-стекла составляет 1140-1185 °С. Температура плавления составляет 1050-1064ы плавления. В отличие от своего экологически чистого аналога борсодержащие волокна из Е-стекла имеют более низкую на 110 °С температуру получения, которая составляет 1250-1264 °С, а температуру плавления 1146-1180 °С. Температуры размягчения для волокон на основе борсодержащих Е-стекол и Е-стекол без оксида бора составляют 830-860 °С и около 916 °С соответственно. Более высокая температура получения экологически чистых стеклянных волокон на основе Е-стекла приводит к росту потребления энергоресурсов для их получения, и, как следствие, увеличению стоимости.
СвойстваМеханические свойства обоих видов волокон на основе Е-стекла почти одинаковы. Прочность на разрыв составляет 3100-3800 МПа. Однако модуль упругости у волокон без оксида бора несколько выше (80-81 ГПа), чем у обычных волокон (76-78 ГПа). Основным отличием стекловолокна марки Е без бора является более чем в 7 раз большая кислотостойкость (выдержка при комнатной температуре в течение 24 часов в 10% растворе серной кислоты). По своей кислотостойкости эти волокна приближаются к химически стойким волокнам на основе ECR стекла.
Плотность борсодержащих стеклянных волокон несколько ниже (2,55 г/см3) по сравнению со своим экологически чистым аналогом (2,62 г/см3). Плотность Е-стекла выше, чем у стекол других типов (за исключением ECR стекла).
С увеличением содержания бора в таких стеклах уменьшается коэффициент преломления и коэффициент линейного расширения. Не содержащие бор Е-стекла имеют более высокую диэлектрическую постоянную, которая при комнатной температуре и частоте 1 МГц составляет 7. Поэтому борсодержащие волокна чаще используют при производстве электронных плат и в аэрокосмической промышленности. В широком производстве композитов эта разница не имеет такого критического значения.
Стекло S
Впервые химический состав стекла под маркой S-glass был запатентован компанией Owens Corning в 1968 (патент 3402055). В состав этого стекла входило 55-79,9 % SiO2, 12,6-32 % Al2O3, 4-20 % MgO. Создание стекловолокна марки S было вызвано бурным развитием композиционных материалов в США в то время и, как следствие, необходимостью созданию стекловолокна с высокими прочностью и модулем упругости. В настоящее время стекло под этой маркой получают на основе систем SiO2-Al2O3-MgO или SiO2-A2O3-MgO-CaO. В исключительных случаях в S-стекло добавляют BeO2, TiO2, ZrO2.
Особенности полученияБлагодаря высокому содержанию тугоплавких оксидов S-стекло имеет очень высокую температуру размягчения 1015-1050 °С. Соответственно высокими являются и температура получения волокон – около 1200 °С, что сопоставимо со стекловолокном марки AR.
СвойстваСтекловолокно марки S обладает рекордными значениями прочности и модуля упругости для данного класса материалов. Лучшая продукция из S-стекла ничем не уступает по своему качеству углеродному волокну и также как и последнее применяется в основном в аэрокосмической области. Прочность волокон при комнатной температуре составляет 4500-4800 МПа, модуль упругости – 86-87 ГПа, прочность лучших образцов волокна марки ВМП – до 7000 МПа.
Стекло AR
Химический составВ начале 70-х годов английская фирма «Pilkington Brothers» разработала и стала выпускать в промышленных масштабах высоко-циркониевое стеклянное волокно Cemfil для армирования цемента. Впоследствии эта марка перешла компании Saint-gobain, в настоящее время основным производителем стекловолокна на основе стекла AR является компания OwensConing и японскаякомпания Nippon electric glass. Щелочестойкие стекла выпускают на основе системы ZrO2-SiO2-Na2O. Содержание дорогого оксида циркония в них варьируется в пределах 15-23 %. Поскольку температура плавления чистого оксида циркония достаточно высока (2715 С), в стекло добавляют значительное количество щелочных металлов, чаще всего Na2O 18-21 %.
Особенности полученияТугоплавкие составы значительно усложняют технологию производства волокна, кроме того, цирконий-содержащее сырье дефицитно и дорого для изготовления массовой продукции. Поэтому вопрос совершенствования составов стекол для армирования цемента продолжает оставаться актуальным. Температура получения волокон из AR-стекла составляет 1280-1320 °С, температура плавления – 1180-1200 °С.
СвойстваПрочность на разрыв волокон на основе AR-стекла довольно низка и составляет около 1500-1700 МПа. Модуль упругости 72-74 ГПа. Такие волокна самые тяжелые среди всех видов стекловолокна, их плотность составляет около 2,7 г/см3.
Поскольку основной областью применения волокон на основе AR-стекла является армирование цементов и бетонов, то основной характеристикой таких волокон является их устойчивость в щелочной среде. Потеря массы после кипячения в насыщенном растворе NaOH для волокон на основе AR-стекла составляет 2-3 %. Для сравнения эта же характеристика для базальтовых волокон составляет 6-7 %.
Стекло ECR
Химический составВпервые стекловолокно под маркой ECR-glass (в некоторых источниках оно указано как химически стойкое Е-стекло) стали выпускать в 1974 г. Это стекло имеет в своем составе до 3 % TiO2 и до 3 % ZnO. Совершенно некорректно называть это стекло разновидностью Е- стекла, поскольку, согласно требованиям международных стандартов, Е-стекло вообще не должно содержать оксида циркония, и к тому же содержание TiO2 в ECR стеклах превышает положенные 1,5 %. Стекловолокно на основе ECR стекла не содержит в своем составе оксида бора, что положительно сказывается на экологичности производства. Зачастую в состав стекловолокна ECR вводят до 3 % Li2O.
Особенности полученияОксид титана является плавнем, его значительное содержание приводит к заметному уменьшению вязкости стекла и, как следствие, температуры получения волокон. Оксид циркония положительно влияет на химическую стойкость стекла. Температура формования волокон на основе ECR стекла составляет около 1218 °С, что меньше, чем у стекловолокна на основе Е-стекла. В то же время для стекол с высоким содержанием оксида лития температура получения волокон выше, чем у стекловолокна Е и составляет около 1235 °С. Фактически это означает, что оксид цинка является более эффективным плавнем, чем оксид бора, к тому же более экологичен и придает дополнительно полезные свойства стекловолокну.
СвойстваСтекловолокно ECR было разработано специально для использования в агрессивных средах, например устойчивость в кислых средах в 4-5 раз выше. При этом прочность этих волокон остается на уровне стекловолокна Е и составляет порядка 2800-3000 МПа, модуль упругости около 80-83 ГПа. Несмотря на то, что плавление и выработка волокна из ECR проводят при более низких температурах его стоимость превышает стоимость стекловолокна Е из-за наличия дорогих компонентов.
Стекло D
В настоящее время волокна из D-стекла являются больше экзотикой, чем реальным продуктом на рынке стекловолокна, поскольку многие производители плат предпочитают использовать вместо них альтернативные виды стекловолокна. Например, сверхчистые кварцевые волокна, полые волокна из Е-стекла также обладают более низкими диэлектрическими характеристиками, чем широко распространенное стекловолокно Е. Однако, у кварцевых волокон меньше модуль упругости, что важно при изготовлении печатных плат, а полые волокна теряют свои диэлектрические свойства в условиях высокой влажности.
Химический составЗачастую в электронной промышленности требуются материалы с очень низкими показателями диэлектрической проницаемости. Электрические свойства волокон определяются такими свойствами как удельное объемное сопротивление, поверхностная проводимость, диэлектрическая постоянная и тангенс угла диэлектрических потерь. В большинстве случаев при производстве плат в качестве армирующего наполнителя используют Е-стекло, однако уменьшение размеров печатных плат предъявляет повышенные требования к стекловолокну. Для решения этой проблемы было разработаны составы стекол марки D. Такие стекла и волокна получают на основе системы SiO2-B2O3-R2O. Содержание в стеклах с низкими диэлектрическими характеристиками оксида кремния достигает 74-75 %, оксида бора – до 20-26 %. Для уменьшения температуры выработки в эту систему добавляют оксиды щелочных металлов (до 3%). Иногда оксид кремния частично замещают на оксид алюминия (до 15 %).
СвойстваВысокое содержание оксида бора приводит к значительному снижению в D-стеклах диэлектрической постоянной и тангенса угла диэлектрических потерь по сравнению с Е- стеклом.
Особенности полученияИз-за высокой стоимости волокна из D-стекла в настоящее время получают только мелкосерийными партиями. Кроме того, высокое содержание в них оксида бора делает их процесс изготовления очень трудным, что связано с высокой летучестью этого компонента в процессе плавления шихты. Температура размягчения D-стекол составляет 770 °С.
Кварцевое стекло
Кварцевые волокна используют в тех случаях, когда требуется значительная термическая стойкость. Кварцевые волокна с содержанием SiO2 менее 95 % (как правило их называют кремнеземные волокна) получают путем путем кислотной обработки волокна алюмоборосиликатного состава, широко применяемого для изготовления бесщелочного волокна, и из силиката натрия с различными добавками. Кремнеземные волокна, полученные выщелачиванием волокон из горных пород, не уступают кремнеземным волокнам, выпускаемым промышленностью. Температура применения кремнеземных волокон 1200 °С.
Сверхчистые кварцевые волокна (содержание SiO2 более 99 %) получают методом сухого формования из водного раствора жидкого стекла. Такие волокна выпускаются под торговой маркой Silfa и используются для теплозащиты. В СССР кварцевые волокна получали по штабиковому способу: вытягиванием нити из капли разогретого конца штабика или путем раздува образующейся капли ацителено-кислородным или кислородно- водородным пламенем. Производство кварцевого волокна может также осуществляться в два приема: получение волокон диаметром 100-200 мк, а затем их раздув потоком раскаленных газов. Волокна собираются на конвейере и формуются либо в виде матов, либо в виде ровницы. Температура плавления таких волокон 1750 °С. При Т = 1450-1500 °С происходит спекание (деформация в твердой фазе), но без размягчения. В условиях длительной эксплуатации и теплосмен, изделия из кварцевого волокна являются стойкими до Т = 1200°С, выше которой у них снижается прочность вследствие кристаллизации.. В настоящее время такие волокна выпускаются под маркой quartztel и astroquartz.
СвойстваСверхчистые кварцевые волокна в основном применяются в аэрокосмической промышленности в тех областях, где требуется высокаятермостойкость. Сочетая высокую термическую стойкость, прочность и радиопрозрачность для ультрафиолетового излучения и излучения с большей длиной волны такие волокна используют для производства обтекателей самолетов.
Использованы материалы из учебного пособия "Стеклянные волокна". С.И. Гутников, Б.И. Лазоряк, Селезнев А.Н.
sammas.ru